Wie man OEE berechnet
In diesem Artikel stellen wir die OEE-Formel vor, schlüsseln ihre drei Komponenten auf, zeigen, wie man die OEE berechnet, und geben ein Beispiel für die OEE-Berechnung.
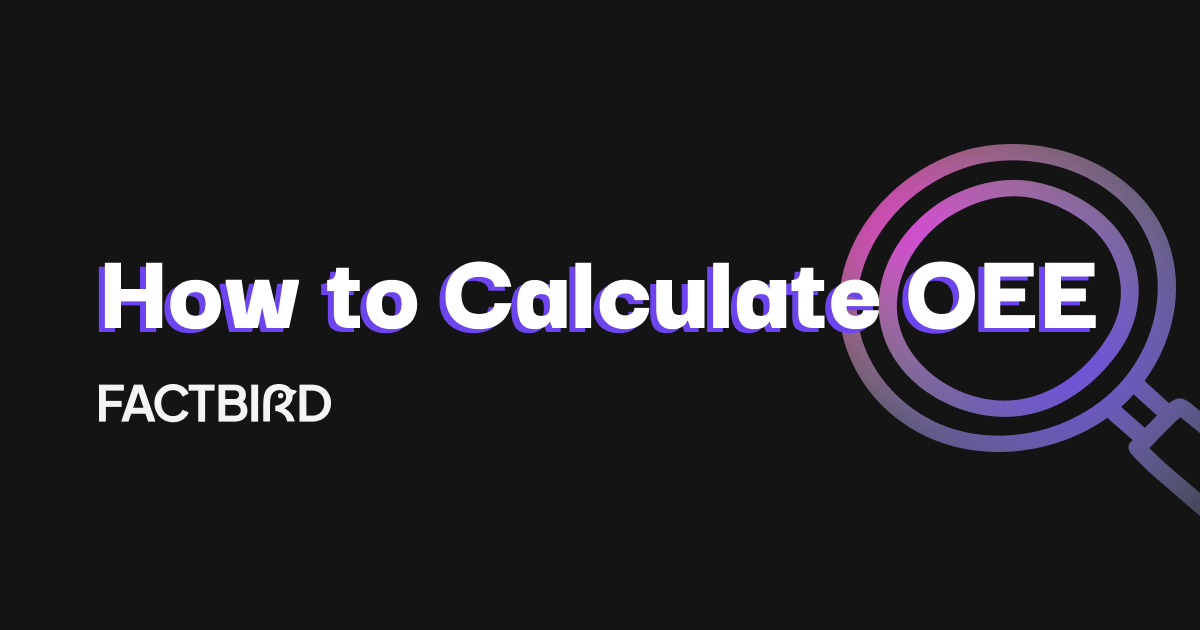
Hersteller, die der kontinuierlichen Verbesserung und der datengesteuerten Entscheidungsfindung keine Priorität einräumen, geraten ins Hintertreffen und verlieren Marktanteile an effizientere Konkurrenten mit niedrigeren Kosten oder effizienteren Produktionslinien.
Die meisten Hersteller haben die Bedeutung von Daten bereits erkannt und streben mit Hilfe der Gesamtanlageneffektivität (Overall Equipment Effectiveness, OEE), einem wichtigen Leistungsindikator für die Verbesserung von Produktionsprozessen, eine Verschlankung an.
OEE-Berechnungen und -Analysen sind für Hersteller ein wirksames Mittel, um neue Effizienzpotenziale zu erschließen, denn sie zeigen deutlich die Bereiche auf, die Aufmerksamkeit erfordern.
In diesem Leitfaden werden wir zwei Methoden zur Berechnung der OEE betrachten, den ursprünglichen Prozess, wie er von Nakajima beschrieben wurde und den modernen OEE-Prozess, den Factbird verwendet.
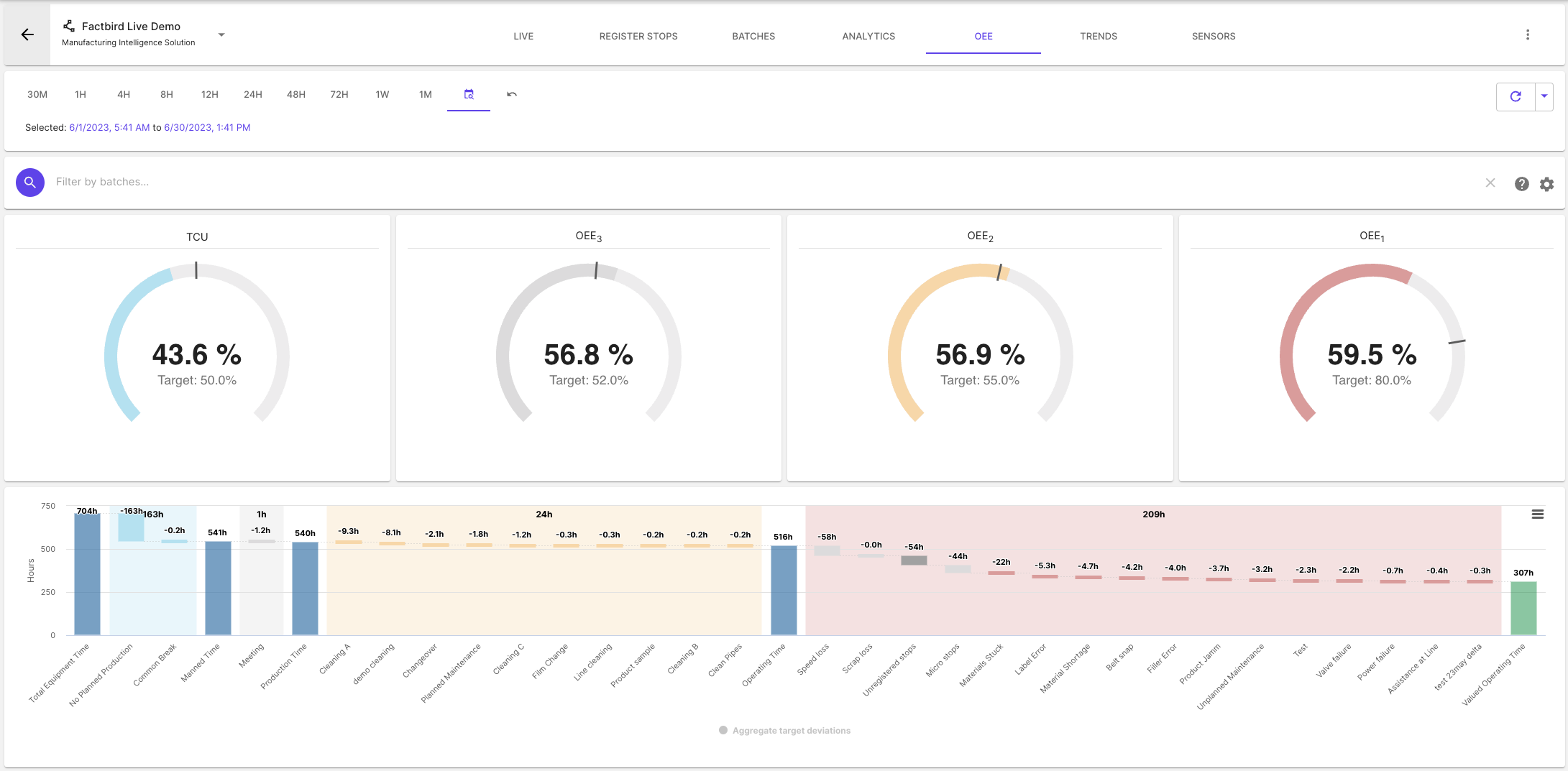
Es gibt mehrere OEE-Berechnungsmethoden
Es gibt mehrere Möglichkeiten zur Berechnung der OEE, wobei die Definition von Verlusten und die Zuweisung von Stopp-Ursachen je nach Branche, Anwendungsfall und individueller Präferenz angepasst werden können.
In Einführung in TPM: Total Productive Maintenance" stellte Nakajima das ursprüngliche OEE-Konzept vor. Ursprünglich konzentrierte sich Nakajimi auf die geplante Produktionszeit und regte nicht an, Faktoren wie geplante Instandhaltung und geplante Umstellungen einzubeziehen. Seitdem haben Hersteller und Lean-Spezialisten neue OEE-Berechnungen vorgelegt, die mehr Verluste erfassen und besser für moderne Fertigungsprozesse geeignet sind.
Schauen wir uns die OEE-Berechnung nach Nakajima an, gefolgt von der OEE-Technik, die von Factbird und führenden Herstellern weltweit verwendet wird.
Die Nakajima TPM OEE Berechnung
OEE ist ein Maß für die Gesamtanlagenleistung, das zur Ermittlung von Verlusten und zur Verbesserung der Gesamtanlagenleistung verwendet wird.
Die von Nakajima aufgestellte Standard-OEE-Formel sieht wie folgt aus:
Gesamtanlageneffektivität (OEE) = Verfügbarkeit x Leistung x Qualität.
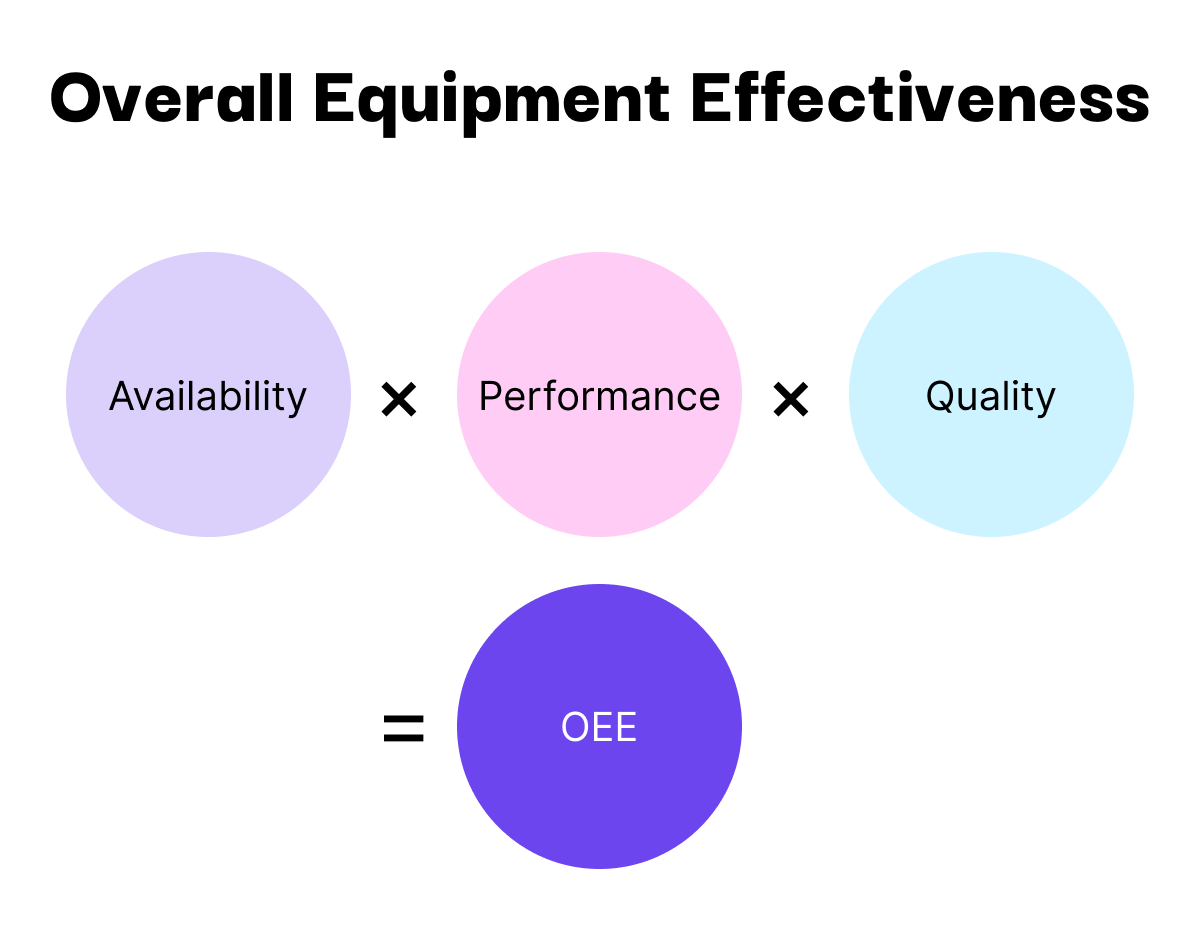
OEE-Komponente 1: Verfügbarkeit
Laut Nakajima wird die Verfügbarkeit durch Ausfallzeiten beeinträchtigt:
- Ausfall der Ausrüstung
- Einrichtung und Einstellung
Im Folgenden wird erläutert, wie die Verfügbarkeitsrate in der OEE nach Nakajima berechnet wird:
- Verfügbarkeitsrate = (Betriebszeit / Ladezeit) x 100
Die Ladezeit wird oft als geplante Produktionszeit bezeichnet, um die Übersichtlichkeit zu erhöhen. Es ist wichtig zu beachten, dass geplante Produktionsstillstände (wie Reinigung und Teambesprechungen) nicht zur Betriebszeit zählen.
Hier ist Operationszeit:
- Betriebszeit = Ladezeit (auch geplante Produktionszeit) - Stillstandszeit
OEE-Komponente 2: Leistung
Die Leistungseffizienz wird durch Geschwindigkeitsverluste beeinträchtigt:
- Leerlauf und kleinere Stillstände
- Reduzierte Geschwindigkeit
Die Leistungseffizienz kann definiert werden als die Betriebsgeschwindigkeitsrate (ideale Zykluszeit / tatsächliche Zykluszeit) multipliziert mit der Netto-Betriebsrate ((verarbeitete Menge x tatsächliche Zykluszeit) / Betriebszeit).
Bei dieser Berechnung wird also die Diskrepanz zwischen der idealen Geschwindigkeit, die sich aus der Konstruktion des Geräts ergibt, und der tatsächlichen Betriebsgeschwindigkeit berücksichtigt.
Hier erfahren Sie, wie Sie die Leistungseffizienz berechnen können:
- Leistungseffizienz = ((Ideale Zykluszeit x Verarbeitete Menge) / Betriebszeit) x 100
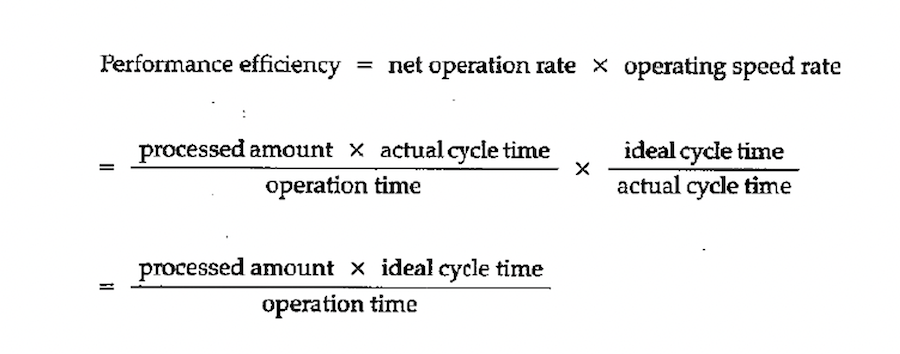
OEE-Komponente 3: Qualität
Die letzte Komponente der OEE-Berechnung ist die Qualität, die den Anteil des Produktionsdurchsatzes, der die geforderten Spezifikationen erfüllt, im Vergleich zum gesamten Produktionsdurchsatz misst.
Bei den Qualitätsverlusten gibt es zwei Kategorien:
- Defekte im Prozess (z. B. Geräte, die eine Aufwärmzeit benötigen und dadurch Defekte verursachen, bis sie einen stabilen Zustand erreichen)
- Geringerer Ertrag (hier zielt die Qualität auf eine "Right First Time"-Produktion ab)
Hier erfahren Sie, wie Sie die Qualitätsrate in OEE berechnen:
- Qualitätsrate = ((bearbeitete Menge - Fehlermenge) / bearbeitete Menge) x 100
Auch ausgedrückt als:
- Qualitätsrate = (Right First Time / Gesamtproduktion) x 100
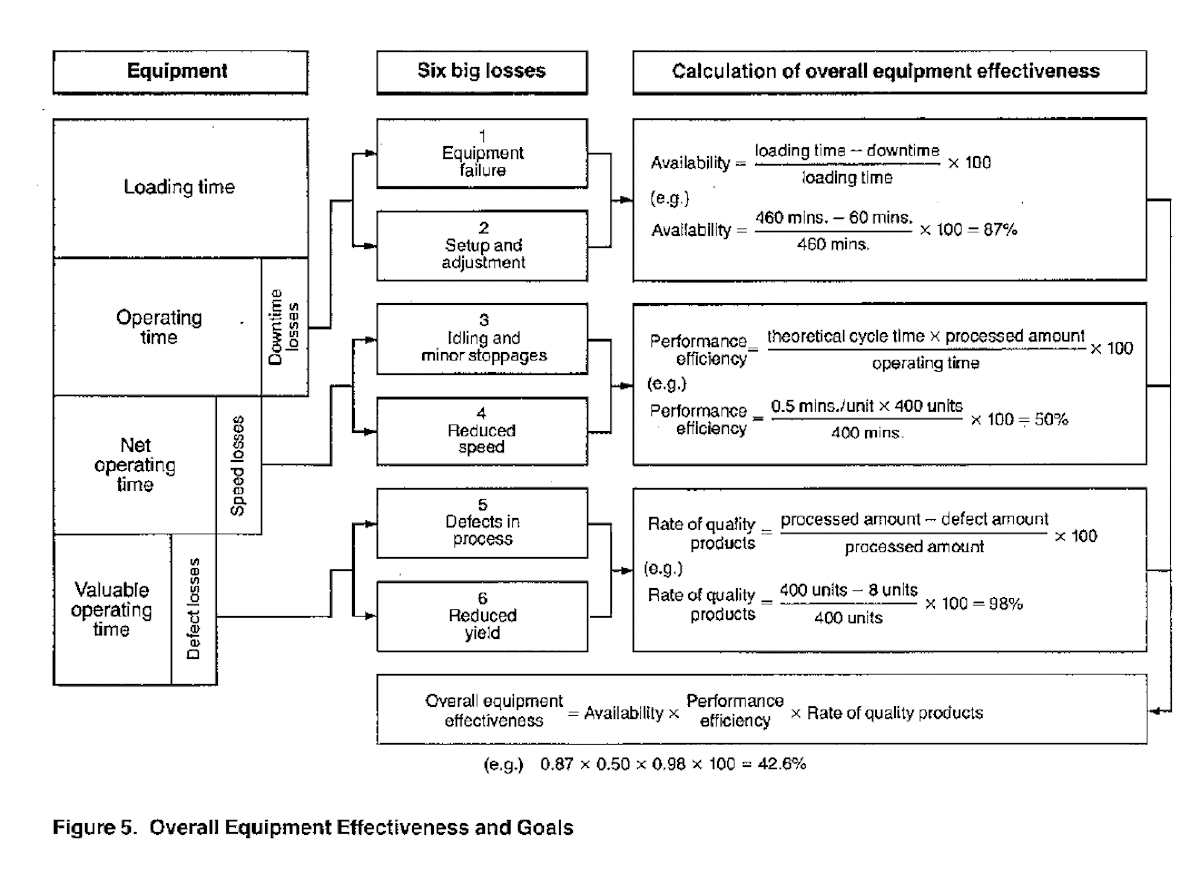
Der OEE-Wasserfall von Factbird
Sehen wir uns an, wie Factbird Herstellern hilft, ihre OEE-Ziele zu erreichen, indem es den Wasserfall-Ansatz für OEE verwendet.
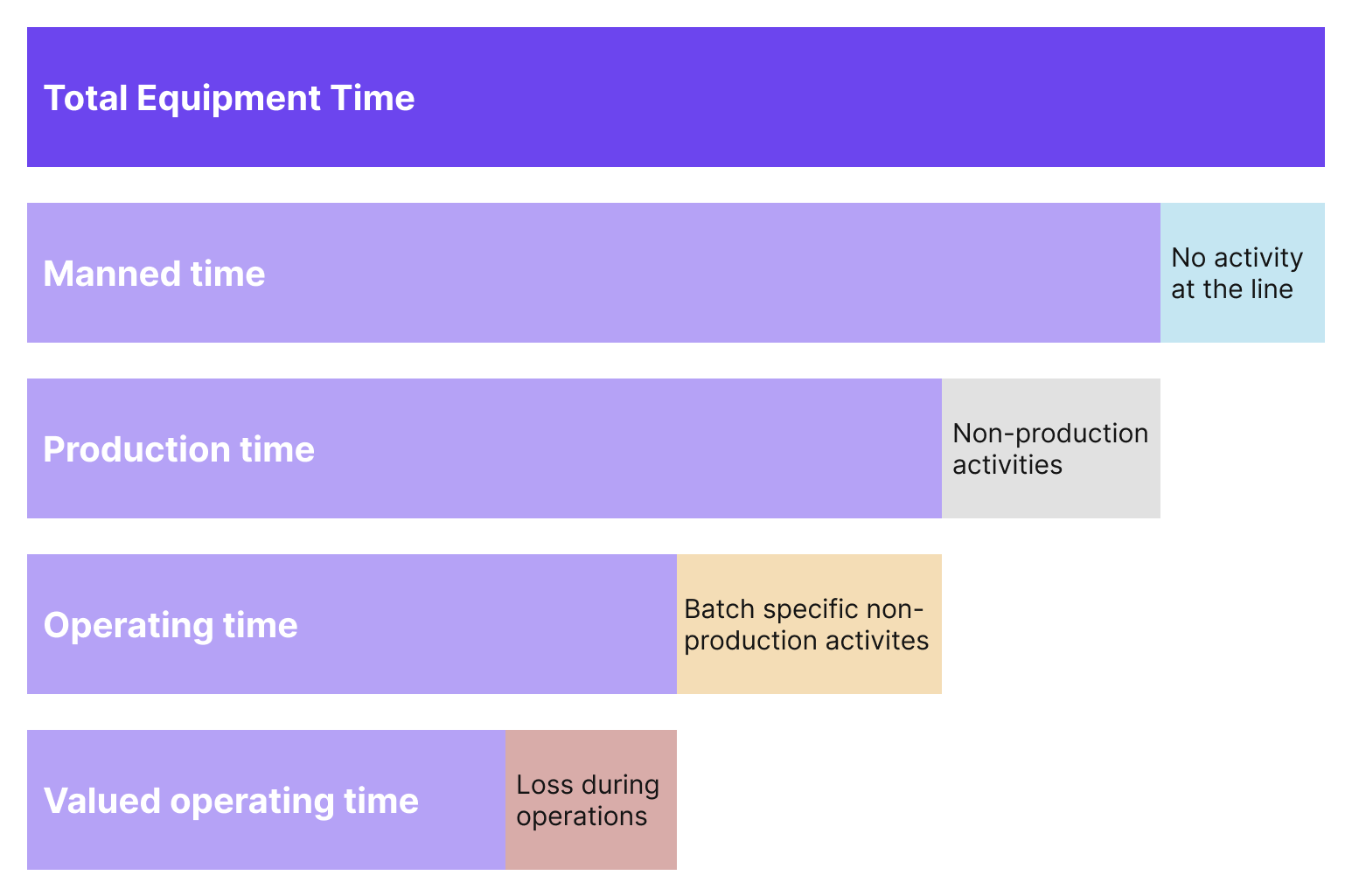
Wie Sie sehen, fügen wir der Nakajima-Berechnung der OEE eine weitere Ebene hinzu, die uns hilft, geplante Ausfallzeiten zu berücksichtigen, die so genannte Total Equipment Time (die gesamte potenzielle Betriebszeit der Anlage).
Das bedeutet, dass die Hersteller die unbemannten produktionsfreien Zeiten, die z. B. durch einen Mangel an Aufträgen oder nur eine Schicht pro Tag entstehen, noch herausrechnen können.
Sie werden feststellen, dass es bei der Wasserfallmethode einfacher ist, Engpässe zu erkennen und Ursachen zu beseitigen, die sich am stärksten auf die Effizienz auswirken, als bei der Formelmethode.
OEE1 vs. OEE2 vs. OEE3 vs. TCU
Die Gesamtkapazitätsauslastung (Total Capacity Utilization, TCU) berücksichtigt geplante Ausfallzeiten aufgrund von Urlauben, Pausen oder einfach keiner geplanten Produktion.
OEE3 berücksichtigt alle geplanten Wartungsarbeiten. In der Regel wird diese Zeit auf die Wochenenden verteilt, da die Anlagen laut Zeitplan nur ein Drittel ihrer durchschnittlichen Laufzeit haben. Wir nennen dies Nicht-Produktionsaktivitäten.
Beispiele für OEE3-Stoppursachen:
- Geplante Wartung
- Qualitätskontrollen
- Personalaktivitäten (z. B. Sitzungen, Schulungen)
OEE2 bezieht sich auf die Zeit, in der eine Produktionslinie aufgrund von Chargenwechseln, Nachschub und Reinigung nicht läuft. Obwohl diese Unterbrechungen geplant sind, nehmen sie einen erheblichen Teil der verfügbaren Gesamtzeit in Anspruch. Wir bezeichnen dies als chargenspezifischen Nichtbetrieb.
Mögliche Ursachen für den OEE2-Stopp sind:
- Chargenumstellung (d. h. Vorbereitung, Umrüsten usw.)
- Wiederbeschaffung (d. h. Material, Verpackung, Etiketten)
- Reinigung (z. B. Reinigung am Ende der Schicht)
OEE1 ist mit der tatsächlich erwarteten Laufzeit verbunden. Dieser Wert steht im Zusammenhang mit ungeplanten Stopps oder langsamen Zyklen. OEE 1 umfasst die Ausfallzeit, die Zykluszeit und den Produktionsabfall/Schrott. Wir nennen dies Verlust während des Betriebs.
Mögliche Ursachen für den OEE1-Stopp sind:
- Maschinelle Mängel
- Prozessfehler
- Wartezeit (z. B. Material, Personal)
- IT-bezogene Ursachen
- Ungeplante Reinigung, z.B. nach einem Defekt
Das OEE-Überwachungssystem von Factbird
Im folgenden Video können Sie sich eine Demo von OEE1, OEE2, OEE3 und TCU in Aktion ansehen.
Ein Beispiel für eine OEE-Berechnung
Lassen Sie uns das bisher Erforschte nun mit einem OEE-Berechnungsbeispiel unter Verwendung der OEE-Methodik von Factbird zusammenfassen.
Ausrüstung insgesamt Zeit
- 7 Tage à 24 Stunden = 168 Stunden
Verfügbarkeitsverluste
Keine Aktivität an der Linie:
- Außerplanmäßige Stunden = 56 Stunden
Nicht-produktive Tätigkeiten:
- Geplante Wartung = 8 Stunden
- Validierung der Ausrüstung = 4 Stunden
- Prüfung neuer Produkte = 2 Stunden
Chargenspezifische Nicht-Produktionstätigkeiten:
- Umstellung und Einrichtung = 17 Stunden
- Tägliche Reinigung = 7 Stunden
Verfügbarkeitsrate = 74 / 168 = 0,44
Geschwindigkeitsverluste
- Validierte Höchstgeschwindigkeit = 240 Stück / min
- Tatsächliche Geschwindigkeit = 161 Stück / min
Leistungsrate = 161 / 240 = 0,67
Qualitätsverluste
- Chargengröße = 100.000 Stück
- Schrott pro Charge = 5.000 Stück
Qualitätsquote = 95.000 / 100.000 = 0,95
All dies zusammen ergibt die Gesamtkapazitätsauslastung:
TCU = 0,44 x 0,67 x 0,95 = 28%
Bei der Berechnung von TCU, OEE3, OEE2 und OEE1 sehen die gleichen Daten etwa so aus:
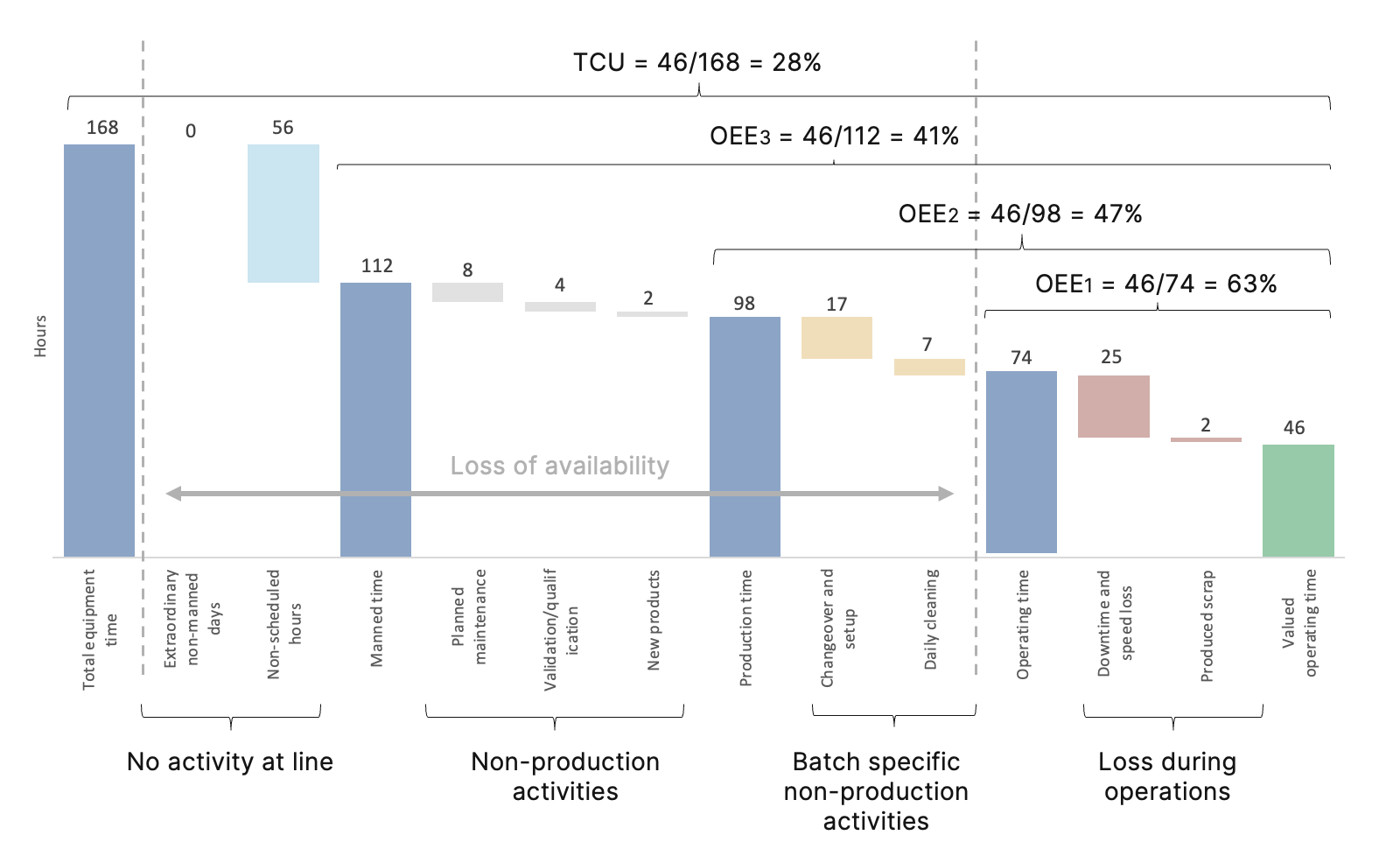
Beachten Sie, dass "Verluste während des Betriebs" in der Wasserfallberechnung als Zeitverluste berechnet wurden, im Gegensatz zu stückbezogenem Ausschuss und Qualitätsverlusten. Dies ist ein gutes Beispiel für unterschiedliche Berechnungsmethoden, die zum gleichen Ergebnis führen.
Häufige Probleme bei OEE-Berechnungen
Obwohl Factbirds Manufacturing Intelligence-Lösungen einfach einzurichten sind und schnell präzise OEE-Berechnungen liefern, gibt es einige häufige Probleme, die sich in jeder Phase der Berechnung einschleichen.
- Zu viele Stopps ausschließen: Mikrostopps nehmen mehr Zeit in Anspruch, als wir normalerweise schätzen. Deshalb ist es wichtig, sie als Ganzes zu analysieren, damit wir die verbesserungswürdigen Bereiche besser priorisieren können.
- Ignorieren oder Unterschätzen der Umstellungszeit: Sie schätzen vielleicht 30 Minuten für Umstellungen, die 40 Minuten oder mehr dauern. Diese Schätzungen summieren sich schnell und stellen große Fehlkalkulationen bei der Produktionsverfügbarkeit dar.
- Unterschätzung der idealen Produktionsgeschwindigkeit: Um dieses potenzielle Problem zu lösen, sollten die Hersteller die von den Maschinenherstellern angegebene validierte Geschwindigkeit berücksichtigen oder mit der höchsten in der Anlage erfassten Geschwindigkeit arbeiten.
- Vergessen Sie, Nacharbeit auszuschließen: Denken Sie daran, den Durchsatz, der nachbearbeitet werden muss, von der Right-First-Time-Zählung auszuschließen. Das steht zwar im Namen, kann aber leicht übersehen werden.
- Ungenaue Ausschusszählungen: Das häufigste Problem bei der Qualitätsmessung im Rahmen der OEE ist die Ausschusszählung. Dies ist in der Regel ein zeitaufwändiger Prozess, der von Bedienern durchgeführt wird und anfällig für menschliche Fehler ist.
Glücklicherweise lassen sich diese Probleme dank moderner Lösungen und professioneller Änderungsmanagementdienste lösen.
Nehmen Sie zum Beispiel das Zählen von Ausschuss. Sie können den Ausschuss automatisch verfolgen, wenn Sie IIoT-Datensammler wie Factbird® DUO mit einem Sensor koppeln. Lesen Sie dazu unsere Fallstudie über die Erwin Quarder Group, in der wir zeigen, dass die Ausschussüberwachung die Ausschussrate dank genauer Informationen über die Ausschussursachen reduzieren kann.
Beginnen Sie so schnell wie möglich mit der OEE-Messung
Wie wir gesehen haben, ist die OEE eine Kennzahl, die Hersteller als effektiven Standard für die Effizienz in der Fertigung verwenden. Der erste Schritt zur Verbesserung der Produktionsleistung ist die Sicherstellung genauer Berechnungen und tiefgreifender Analysen der OEE.
Wenn Sie sich nicht sicher sind, wie Sie mit der Datenerfassung in den Betrieben beginnen sollen, lesen Sie unseren 5-Schritte-Leitfaden zur Datenerfassung in der Fertigung.
Wir hoffen, dass diese Erklärung der OEE-Berechnung Ihnen bei der Berechnung der OEE in Ihren eigenen Produktionslinien hilft. Wenn Sie das Gefühl haben, dass Sie Hilfe bei den ersten Schritten benötigen oder Fragen zur OEE-Messung in der Produktion haben, kontaktieren Sie uns einfach für einen unverbindlichen Chat.