Berechnung des Durchsatzes: Ein Leitfaden zur Steigerung der Produktionsleistung
Die Schätzung der Effizienz Ihrer Fabrik umfasst eine Vielzahl von Elementen, aber der Durchsatz ist nach wie vor die Kennzahl, die den Wettbewerbsvorteil ausmacht.
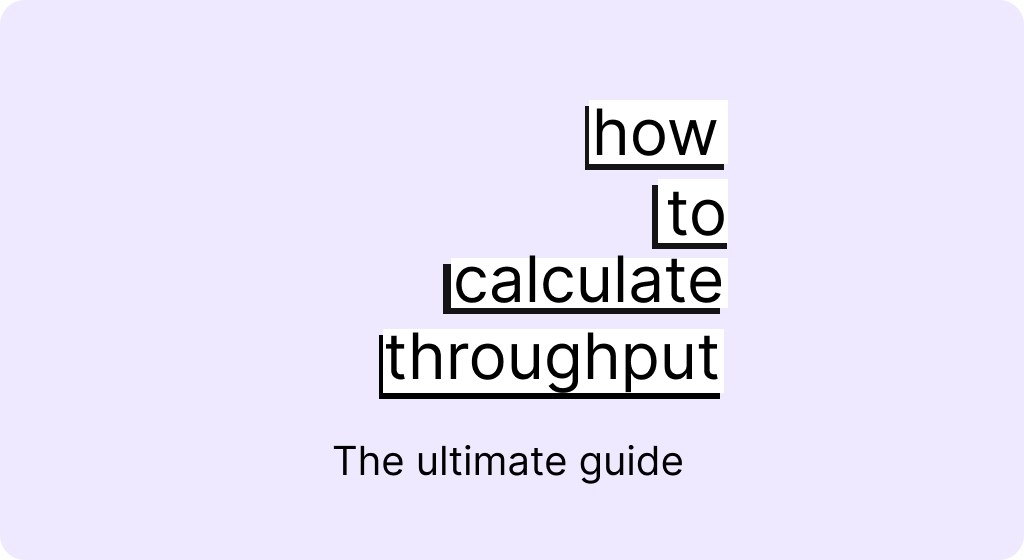
Die Schätzung der Effizienz Ihrer Fabrik umfasst eine Vielzahl von Elementen, aber der Durchsatz ist nach wie vor die Kennzahl, die einen Wettbewerbsvorteil definiert. Er ist so relevant, dass OEE-Berechnungen Aufschluss darüber geben, ob der potenzielle Durchsatz der Fabrik eingeschränkt ist. Aus diesem Grund wirkt sich der Durchsatz direkt auf die Ertragsrate aus und beeinflusst die Strategien für anstehende Investitionen.
In diesem Leitfaden wird eine Methode zur Berechnung des Durchsatzes und der verschiedenen Variablen vorgestellt, die seine Bedeutung im Produktionsalltag bestimmen.
Was ist Durchsatz?
Die Durchsatzrate ist die Kennzahl, mit der wir die Geschwindigkeit messen, mit der sich Einheiten durch den Produktionsprozess bewegen, vom Startpunkt bis zur fertigen Einheit. Sie kann eine Reihe von Elementen umfassen, vom Rohstofftransport über die Materialverarbeitung, die Entwicklung einzelner Teile, die Montage von Einheiten, die Interaktion mit dem Bedienpersonal, den Input des Kunden (im Falle einer Sonderanfertigung) usw.
Für die Berechnung der Durchsatzrate sind zwei Elemente maßgeblich:
Vorrat (I): Hierbei handelt es sich um die Anzahl der Einheiten in der Fertigung und nicht um die fertigen Produkte, die zur Auslieferung gelangen. Dies mag etwas schwierig zu verstehen sein, da es die typische Zählung des "fertigen, verkaufsfertigen Produkts" verschiebt und auch die Einheiten in der Produktionsphase aufführt.
Durchlaufzeit (T): Die Zeit, die ein Produkt von Anfang bis Ende in der Produktion verbringt. Die Durchlaufzeit ist die Summe von vier verschiedenen Intervallen:
- Bearbeitungszeit: Die für die eigentliche Produktion aufgewendete Zeit. Umfasst alle Schritte vom Rohmaterial über die Montage bis zum fertigen Produkt.
- Inspektionszeit: Je nach Branche kann sich die Inspektionszeit drastisch ändern, da sie Belastungstests, visuelle Qualitätstests, Geschmacks- und Geruchstests (für die Lebensmittel- und Getränkeindustrie) usw. erfordern kann. Es handelt sich um die Gesamtzeit, die für die Prüfung von Komponenten und Unterbaugruppen im Fertigungsprozess benötigt wird.
- Bewegungszeit: Dies hängt ebenfalls von der Branche ab, vor allem aber davon, wie modern der Maschinenpark ist, um die Bewegungs- und Bereitstellungsprozesse zu minimieren. Die Bewegungszeit umfasst die Zeit, in der Unterbaugruppen zwischen den Arbeitsstationen bewegt werden.
- Wartezeit: Die Zeit, die eine Einheit in der Warteschlange verbringt, um bearbeitet, inspiziert oder bewegt zu werden, entweder ein fertiges Produkt oder eine Unterbaugruppe. Hängt in der Regel davon ab, wie komplex der Produktionsprozess ist.
Die Bedeutung der Berechnung des Durchsatzes
Die Ermittlung des tatsächlichen Durchsatzes, den Fabriken produzieren, ist von entscheidender Bedeutung, um eine Gewinnmaximierung zu gewährleisten und die Produktionsabläufe zu verbessern. Vier Aspekte helfen uns, die Bedeutung der Durchsatzberechnung zu verstehen.
In erster Linie hilft uns die Kenntnis der tatsächlichen Produktionszeit dabei, die Engpässe zu ermitteln. Dies ist ein iterativer Prozess, da sich Engpässe von Periode zu Periode ändern können. Einige Ursachen könnten mit den Maschinen zusammenhängen, wofür eine Produktionssoftware eine Lösung darstellt. In anderen Fällen werden durch umfassende Analysen unzureichende Prozesse der Bediener aufgedeckt.
Was den letzten Punkt betrifft, so lassen sich Ineffizienzen leicht beheben, wenn die Maschinen nicht mit ihrer maximalen Kapazität arbeiten. Dies kann eine Änderung der Inspektionszeiten, eine Verkürzung der Zeiträume zwischen den geplanten Wartungsarbeiten oder eine völlige Änderung der Strategie erfordern.
Die Umsetzung von Methoden für eine optimale Produktion kann in manchen Fällen anstrengend erscheinen, aber wenn man schnelle Ergebnisse sieht, kann sich das Unternehmen mit diesen Werten identifizieren. Eine adäquate Berechnung der Durchsatzrate ist bei schlanken Fertigungsprozessen erforderlich, da weniger Zeit in der Produktion verbracht wird und somit mehr Zeit für die Optimierung anderer Prozesse bleibt.
Nehmen wir schließlich an, wir wollen Ineffizienzen verringern. In diesem Fall besteht ein Schlüsselelement der Durchsatzberechnung darin, dass durch die Verringerung der Produktionszeit die Betriebszeit der Maschinen reduziert wird, was wiederum zu einer Verringerung der Energiekosten und der zusätzlichen Arbeitsstunden für das Personal führt. Die Verringerung des Materialabfalls ist eine weitere Nebenfolge dieser Optimierungsphase.
Zykluszeit vs. Durchlaufzeit
Die Zykluszeit ist zwar verwandt, misst aber die Arbeitszeit von Anfang bis Ende für eine Einheit, während die Durchlaufzeit die gesamte Prozesszeit einschließlich der Warteschlangen misst.
In der praktischen Anwendung wird die Zykluszeit verwendet, wenn Ihre Maschinen innerhalb der Erwartungen arbeiten. Im Gegensatz dazu sollte die Durchlaufzeit verwendet werden, wenn es zu Verzögerungen kommen kann, da es einfacher ist, die einzelnen Phasen eines Prozesses zu unterbrechen, um ein Produkt herzustellen.
Durchlaufzeit vs. Durchsatzzeit
Im Gegensatz zur Durchlaufzeit ist die Durchlaufzeit eine Kennzahl, die auf der Kundennachfrage basiert. Wir beginnen mit der Zählung der Durchlaufzeit, wenn ein Auftrag erteilt wird, und sie endet, wenn das fertige Produkt den Kunden erreicht. Unternehmen neigen dazu, mit Puffern - Produktbeständen - zu arbeiten, um die Durchlaufzeit drastisch zu reduzieren; andernfalls würde sich eine wahnsinnige Wartezeit pro Kunde bilden. Der Umfang dieser Bestände steht in direktem Zusammenhang mit der Produktionskapazität, der Lagerkapazität, der Verkaufsstrategie und der allgemeinen Produktnachfrage.
Die Durchlaufzeit hingegen umfasst die gesamte Produktionszeit pro Artikel; daher muss zwischen der Chargendurchlaufzeit und der Produktstückzeit unterschieden werden.
Wie wird der Durchsatz berechnet?
Die Durchsatzrate ist relativ einfach zu berechnen, wenn man die genaue Summe der Durchlaufzeit kennt.
T = I / F
Wo:
- T = Durchsatz
- I = Bestandsaufnahme
- F = Fließzeit
Dennoch müssen wir den Unterschied zwischen dem Prozessdurchsatz, der der oben dargestellten Gleichung entspricht, und dem Zeilendurchsatz feststellen .
Der Prozessdurchsatz ist die Anzahl der von Anfang bis Ende produzierten guten Einheiten. Dabei werden Ausschuss und andere Probleme berücksichtigt, die während des Herstellungsprozesses auftreten können, wie z. B.:
- Ausfallzeiten (in Verbindung mit Abbruchursachen)
- Geschwindigkeit der Maschine
- Störung
- Menschliche Faktoren (Bedienerfehler oder falsche Bedienerschulung)
- Mangel an Rohstoffen
Wenn also in einer Fabrik pro Schicht 19.000 Stück produziert werden, aber nur 16.400 Stück auf Anhieb, dann errechnet sich die Durchsatzrate aus 16.400 Stück pro Schicht (8 Stunden), was 2.050 Stück pro Stunde bedeutet. Offensichtlich helfen uns Zahlen, wie in diesem Fall, dabei, Verbesserungsmöglichkeiten in den Fertigungsprozessen zu erkennen.
Der Liniendurchsatz stellt die produzierten Waren pro Linie und Zeiteinheit dar, muss aber die Effizienz berücksichtigen, mit der jede Linie arbeitet. Aus diesem Grund können wir verschiedene Werte für den Liniendurchsatz haben, aber einen Gesamtprozessdurchsatz pro Fertigungsbereich. Der Liniendurchsatz ist wichtig, um die Effizienz der Maschinen zu ermitteln, wenn sie aufgerüstet oder automatisiert werden müssen oder wenn andere relevante Fehler die Effizienz behindern.
Wie man die Durchsatzrate erhöht
Wenn Hersteller ein verstecktes Potenzial in ihren Fabriken entdecken, ist dies eine häufig gestellte Frage. Durchsatzraten können über Erfolg oder Misserfolg entscheiden, wenn es darum geht, Kunden zufrieden zu stellen oder einen Wettbewerbsvorteil auf dem Markt zu bewahren.
In diesem Abschnitt werden wir einige Strategien aufzählen, mit denen Sie Ihre Durchsatzrate für maximale Produktivität erhöhen können.
Strategie Nr. 1 - Beseitigung von Engpässen
Wie Priory bereits erwähnte, lassen sich Engpässe dank der Durchsatzanalyse leicht ermitteln. Prozesse können zu Leerlaufzeiten führen, weil Maschinen nicht richtig funktionieren oder die Mitarbeiter ihre Funktionsweise nicht verstehen. Andere, nicht so offensichtliche Engpässe können mit Verpackungsprozessen oder Maschinen zusammenhängen, die Warteschlangen zwischen Arbeitsplätzen nicht richtig synchronisieren.
Um Engpässe zu beseitigen, müssen Sie Ihre Prozesse im Detail evaluieren. Sie müssen Wege finden, wie die Produktionszeiten durch Optimierung verkürzt werden können, oder einen Prozess ganz eliminieren, um eine kostengünstigere Lösung zu finden.
Strategie #2 - Erhöhung der Verfügbarkeit
Wie wir aus der OEE-Berechnungsformel wissen, ist die Verfügbarkeit eine ihrer Komponenten. Die beiden Verluste bei der Verfügbarkeit sind geplante und ungeplante Stopps. Geplante Stopps sind bei Umrüstungen, für geplante Wartungsarbeiten und manchmal bei Inspektionen erforderlich. Auf die Kategorie der ungeplanten Stopps können wir Einfluss nehmen.
Ein häufiger Fehler, der Maschinen für ungeplante Stillstände anfällig macht, ist das Hinauszögern geplanter Wartungsarbeiten für eine kontinuierliche Produktion. Verschlissene Maschinen oder defekte Ausrüstungsgegenstände gehören zu den Hauptursachen für wiederholte Stillstände.
Schulen Sie Ihre Bediener, damit sie die Fehlerursachen und die Standardverfahren zur Fehlerbehebung registrieren. Das Führen eines historischen Rückstands hilft dabei, sich wiederholende Fehlercodes anzugehen und den Wartungsteams detaillierte Informationen zu liefern.
Strategie Nr. 3 - Verringerung der Ausschussmenge
Um auf das Beispiel der Berechnung der Durchsatzrate zurückzukommen: Wir hatten eine Fabrik, die alle 8 Stunden 19.000 Stück produzierte, von denen 16.400 nach dem Prinzip "right-first-time" der OEE akzeptabel waren. Dies bedeutet, dass 86,31 % der akzeptablen Produktion oder 13,69 % Verschwendung anfallen.
Das Management ist dafür verantwortlich, die Verschwendung in der Produktion zu beseitigen. Wenn Sie also die Ausschussrate um die Hälfte senken, erhalten Sie 1300 Stück mehr pro Schicht. In einer Fabrik mit vier Schichten pro Tag bedeutet das 5200 Stück mehr pro Tag oder 27 % der Produktion einer Schicht. Ja, Zahlen können einem die Botschaft vermitteln, wenn man analysiert, wie viel Produktion aufgrund ineffizienter Herstellungsverfahren buchstäblich verschwendet wird. Anpassungen helfen auch den Finanzen, indem sie die Kosten für die Wiederaufbereitung von Teilen, die Energieverschwendung, den Rohstoffverbrauch und die zusätzlichen Arbeitsstunden für Ihr Personal senken.
Strategie Nr. 4 - Überprüfung der Produktionsabläufe
Es ist unmöglich zu erraten, welche Bereiche verbessert werden sollten, ohne zu wissen, was in der Werkstatt passiert. Beginnen Sie mit der Überprüfung des Personals in den einzelnen Bereichen, um festzustellen, ob die Arbeit automatisiert werden kann oder ob die Fähigkeiten der Mitarbeiter nicht übereinstimmen. Die Kenntnis der wöchentlichen Produktionsziele und des Gesamtarbeitsplans ist unerlässlich, um die Produktionsziele in allen Fabriken aufeinander abzustimmen.
Bewerten Sie diese Aspekte im Hinblick auf die Ausrüstung:
- Status und Arbeitsleistung
- Verfügbarkeit von Ersatzteilen
- Kosten der planmäßigen Wartung
- Bedarf an spezialisierten Wartungsteams
- Möglichkeit der Automatisierung der Produktion
- Einführung von Software zur Produktionsüberwachung
- Investitionen in neue Maschinen
Die dritte Stufe, die sich auf Prozesse bezieht, ist mit Engpässen verbunden. In diesem Punkt können Sie auch den Transport zu den Lagern im Hinblick auf die benötigte Zeit und die benötigten Ressourcen sowie das ideale Produktionsvolumen zur Deckung der Verbrauchernachfrage bewerten.
Strategie Nr. 5 - In Mitarbeiterschulungen investieren
Je besser Ihr Personal vorbereitet ist, desto sicherer kann es bei der Behebung von Störungsursachen und bei der Entscheidungsfindung auf der Grundlage zuverlässiger Daten sein. Die Erfahrung lehrt uns, dass Bediener, die nicht über die erforderliche Ausbildung verfügen, eher zu Produktionsverzögerungen führen, die sich auf die gesamte Lieferkette auswirken.
Entscheiden Sie sich stattdessen für eine Mentalität der kontinuierlichen Verbesserung auf allen Ebenen Ihres Unternehmens. Bereiten Sie regelmäßige Schulungen vor, in denen Sie Ihre Mitarbeiter in neuen Technologien oder Methoden zur Verbesserung bestehender Arbeitsabläufe schulen.
Wie kann Factbird den Unternehmen bei der Durchsatz- und allgemeinen Fertigungsoptimierung helfen?
Die Fertigungsüberwachung bietet Fabriken zahlreiche Vorteile, angefangen bei der Feststellung von Veränderungen in der OEE und den Durchsatzraten, ohne dass hohe Investitionen erforderlich sind. Dank Überwachungslösungen wie Factbird können bestehende Maschinen in Netzwerke integriert werden, um die Produktion zu steigern, wobei das Management oder die Bediener jederzeit auf Informationen zugreifen können. Im Gegenzug müssen die Unternehmen keine großen Summen für eine Produktionssteigerung investieren.
Durch den Einsatz von Industrie 4.0-Technologien können wir detaillierte Informationen über unsere Produktionszahlen abrufen, Engpässe aufdecken, fehlgeschlagene Prozesse wiederholen (dank der Verwendung von Videoüberwachungslösungen wie Factbird View) und Korrekturstrategien entwickeln. Die Automatisierung von Aufgaben, wie z. B. das Zählen von Ausschuss, hilft uns, Talente auf relevantere Positionen zu versetzen und Verzögerungen bei der Verfügbarkeit zu reduzieren.