6 Tipps für eine erfolgreiche OEE-Implementierung
Hersteller können von einer genauen OEE-Messung stark profitieren. Mit diesen sechs Tipps zur OEE-Implementierung und erfolgreichen Fallbeispielen können Sie loslegen.
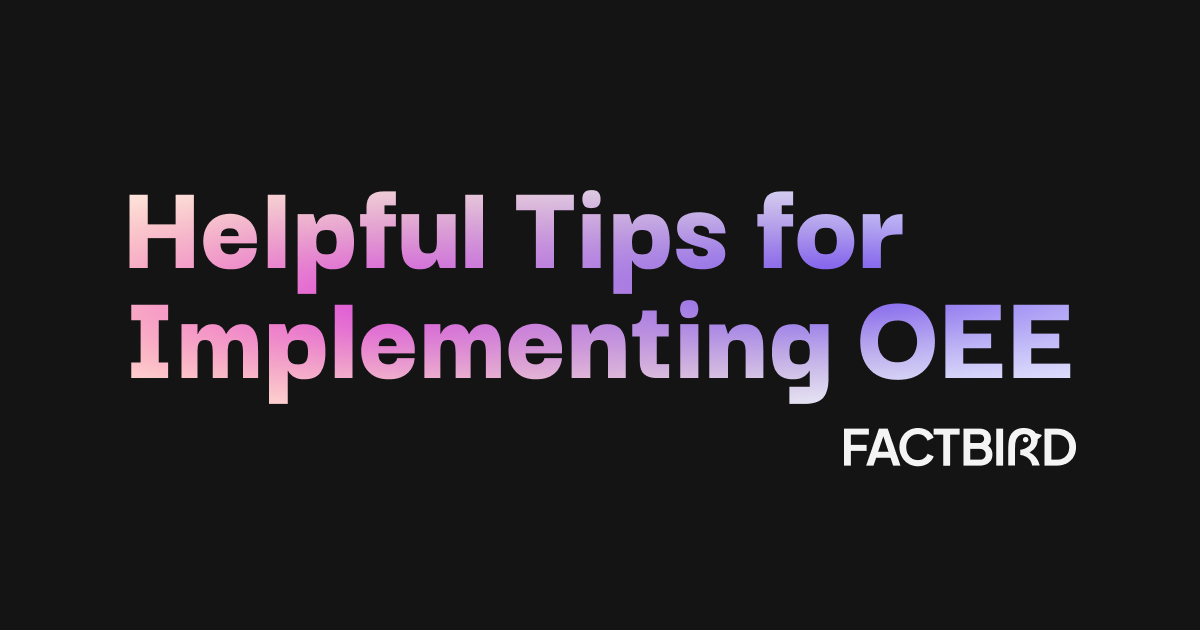
Die Implementierung und Verbesserung der Gesamtanlageneffektivität (Overall Equipment Effectiveness, OEE) ist für Hersteller, die ihre Produktivität und Nachhaltigkeit steigern wollen, von entscheidender Bedeutung.
In diesem Artikel werden praktische Strategien vorgestellt, die Ihnen helfen, die OEE zu implementieren und zu verbessern, um nachhaltige Fertigungsqualität und Rentabilität zu erreichen.
Werfen wir nun einen Blick auf einige Best Practices für die Implementierung von OEE.
1. OEE-Komponenten definieren
Die Umsetzung der OEE beginnt mit einer klaren Definition der drei Schlüsselkomponenten, die in der Regel wie folgt definiert werden:
- Die Verfügbarkeit misst die Betriebszeit der Maschine.
- Die Leistung bewertet die Betriebsgeschwindigkeit im Vergleich zur validierten Geschwindigkeit.
- Die Qualität bewertet das Verhältnis der produzierten Gutteile zur Gesamtzahl der produzierten Teile.
Die genaue und einheitliche Definition dieser Komponenten im gesamten Unternehmen bildet die Grundlage für aussagekräftige OEE-Messungen.
Mehr über die drei Komponenten der OEE erfahren Sie hier: Wie man OEE berechnet.
2. Standardisieren Sie für einen effektiven Vergleich
Ein großes Problem bei der Implementierung von OEE ist, dass die verschiedenen Fabriken oder Bereiche innerhalb eines Unternehmens nicht alle dieselben Standards verwenden. Sie haben unterschiedliche Definitionen von Ausfallzeiten, Leistungsgeschwindigkeit und Qualitätsmängeln, was einen genauen Vergleich der OEE-Ergebnisse erschwert.
Um hier Abhilfe zu schaffen, ist es unerlässlich, eine Standarddefinition für die OEE und ihre Bestandteile zu schaffen, die von allen im Unternehmen verwendet wird. Diese Definition muss in allen Arbeitsbereichen kommuniziert und in die Praxis umgesetzt werden, damit jeder die Anlageneffektivität auf dieselbe Weise misst und konsequent an ihrer Verbesserung arbeitet.
Verbessern Sie die OEE mit der branchenführenden OEE-Software >
3. Definieren Sie Stopp-Kategorien und Stopp-Ursachen
Ein wichtiger Aspekt bei der Implementierung von OEE ist die Definition und Registrierung von Stillstandskategorien und Stillstandsursachen. Diese Kategorien stellen die Ereignisse dar, die zu Ausfallzeiten in Ihrem Fertigungsprozess führen, während die Ursachen die spezifischen Gründe für diese Ereignisse aufzeigen. Durch sorgfältige Definition und Kategorisierung dieser Stopps können Sie verwertbare Erkenntnisse gewinnen, um die OEE effektiv zu verbessern.
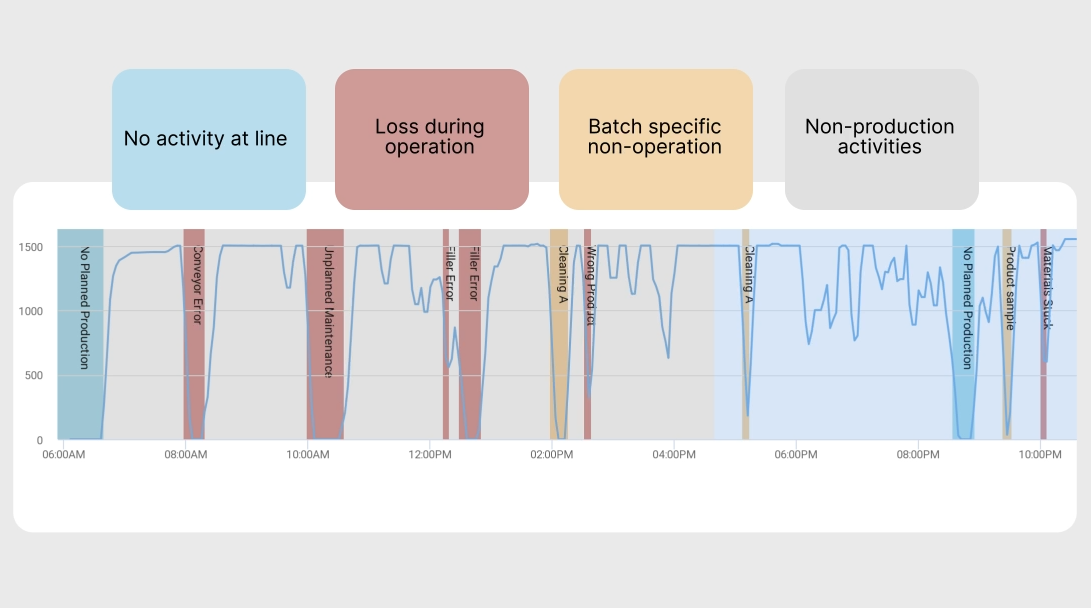
Einfach beginnen, intelligent skalieren
Wir von Factbird empfehlen, mit maximal 20 Hauptursachen für Arbeitsunterbrechungen zu beginnen. Indem Sie mit grundlegenden Kategorien wie "Materialstau" beginnen, halten Sie die Mitarbeiter bei der Stange, stören ihre Arbeit nicht, schaffen gute Gewohnheiten und erfassen nützliche Informationen. Sie können unsere Vorlage für Stoppursachen hier herunterladen, um loszulegen: Laden Sie die OEE Stop Causes Excel-Vorlage herunter (direkter Download).
Verfeinern mit Erfahrung und Daten
Wenn Ihr Unternehmen an Erfahrung gewinnt und Daten sammelt, können Sie die Ursachen für einen Stau verfeinern, indem Sie die anfänglichen übergeordneten Kategorien in spezifischere Ursachen aufschlüsseln. So können Sie z. B. die Unterkategorien "Materialstau" wie "Etikett auf der Rolle eingeklemmt", "Karton im Falzapparat eingeklemmt" oder "Produkt im Extruder eingeklemmt" genauer untersuchen. Diese Granularität ermöglicht ein genaueres Verständnis der Ursachen für den Stillstand.
Abgleich mit OEE- und TCU-Klassifikationen
Um einen umfassenden Überblick über die Faktoren zu erhalten, die sich auf Ihre OEE auswirken, ist es wichtig, Ihre Stoppursachen mit den OEE- und TCU-Klassifikationen abzugleichen. Dabei wird jede Stoppursache danach kategorisiert, ob sie unter Betriebsverluste (OEE1), Chargenumstellungsverluste (OEE2), Verluste durch produktionsfremde Tätigkeiten (OEE3) oder Zeiten ohne Tätigkeit an der Linie (TCU) fällt. Diese Klassifizierung bietet eine differenzierte Sicht auf die verschiedenen Dimensionen Ihrer OEE und ermöglicht es Ihnen, gezielte Maßnahmen zur Verbesserung bestimmter Bereiche zu ergreifen. Mehr dazu erfahren Sie in unserem Artikel zur Berechnung der OEE.
Verwertbare Einblicke freisetzen
Durch die Definition von Stillstandskategorien und -ursachen erhalten Sie wertvolle Einblicke in die Stillstandsereignisse, die in Ihrem Fertigungsprozess auftreten. So können Sie Muster, Trends und wiederkehrende Probleme erkennen, die die Effektivität Ihrer Anlagen beeinträchtigen. Mit diesem Wissen können Sie datengestützte Strategien entwickeln und proaktive Maßnahmen ergreifen, um Ausfallzeiten zu reduzieren, die Leistung zu verbessern und die Gesamtproduktivität zu steigern. Die umsetzbaren Erkenntnisse, die sich aus klar definierten Stillstandskategorien und -ursachen ableiten lassen, dienen als Katalysator für betriebliche Verbesserungen, die Ihr Unternehmen auf dem Weg zur OEE-Exzellenz voranbringen.
4. Daten sammeln und analysieren
Nach der Definition der OEE-Komponenten und der Festlegung einer Standarddefinition besteht der nächste Schritt darin, die relevanten Daten zu sammeln.
Durch den Einsatz innovativer Tools wie Factbird, der weltweit führenden Plug-and-Play-Lösung für Manufacturing Intelligence, wird die Datenerfassung vereinfacht, die Genauigkeit erhöht und die Effizienz verbessert.
Die Erfassung von Daten zu Maschinenbetriebszeit, Produktionsgeschwindigkeit und Qualitätsmetriken ermöglicht die Berechnung von OEE-Werten. Diese Daten dienen als Grundlage für die Ermittlung verbesserungswürdiger Bereiche und das Treffen fundierter Entscheidungen.
Lesen Sie hier mehr darüber, wie Sie mit der Datenerfassung in den Betrieben beginnen können: 5-Schritte-Leitfaden zur Datenerfassung in der Fertigung.
5. Verbesserungswürdige Bereiche identifizieren
Der Hauptvorteil der OEE besteht darin, dass sie Ihnen hilft, die Bereiche zu priorisieren, in denen Sie Verbesserungen vornehmen können.
Sie können die OEE-Kategorien verwenden, um die spezifischen Bereiche zu ermitteln, die Aufmerksamkeit benötigen und in denen die größten Fortschritte erzielt werden können. Dann können Sie Aktionspläne erstellen, um die Dinge zu verbessern. So können Sie Ihre Anlagen optimal nutzen und Verschwendung reduzieren, was zu einer höheren Produktivität führt.
6. Kontinuierliche Verbesserungskultur
Die Umsetzung der OEE ist keine einmalige Aktivität, sondern ein fortlaufender Prozess. Unternehmen, die sich für operative Exzellenz einsetzen, fördern eine Kultur der kontinuierlichen Verbesserung. Dazu gehört die regelmäßige Überprüfung und Verfeinerung der OEE-Messungen, die Analyse von Trends und die Ermittlung von Optimierungsmöglichkeiten.
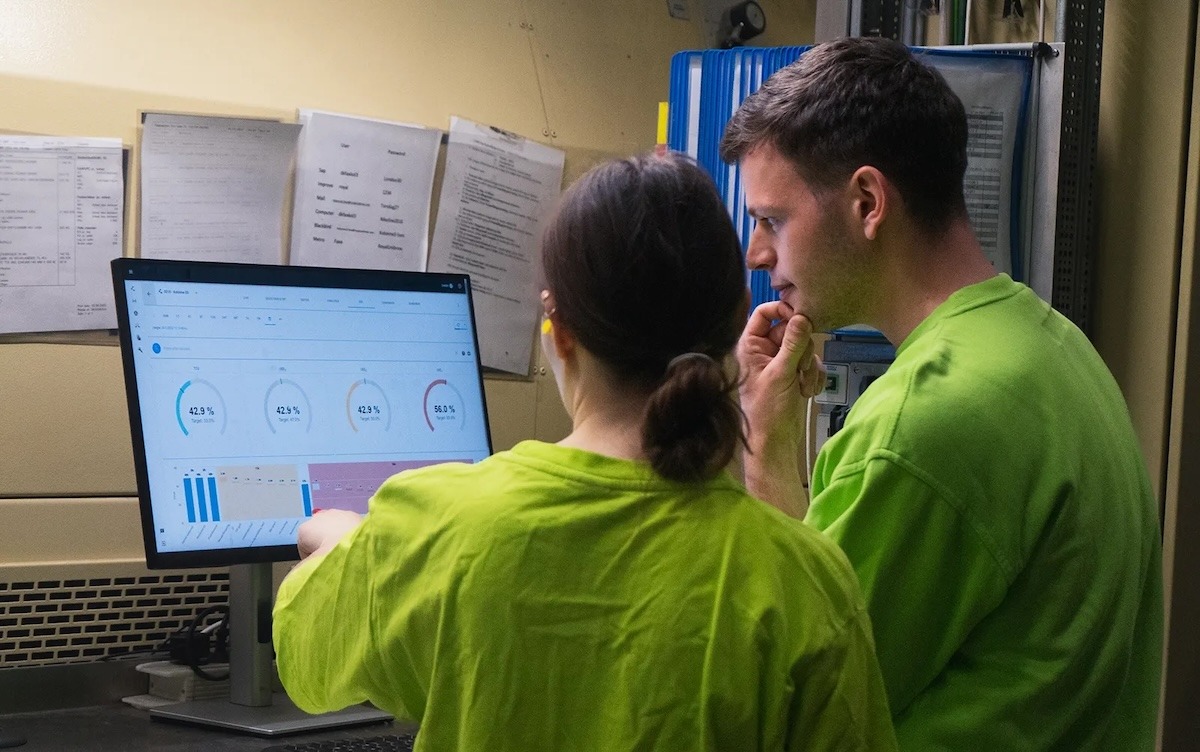
Indem Sie einen datengesteuerten Ansatz verfolgen und Ihre Kollegen kontinuierlich in den Verbesserungsprozess einbeziehen, können Sie nachhaltigere Verbesserungen erzielen, Ihre Teams befähigen und eine höhere operative Qualität erreichen.
OEE-Benchmarks
In Wirklichkeit ist es für jeden Prozess unmöglich, eine OEE von 100 % (auch bekannt als "perfekte Produktion") zu erreichen. Hier ein kurzer Überblick über die Gründe:
- Eine 100%ige Verfügbarkeit ist nur möglich, wenn die Anlagen immer während der geplanten Produktionszeit in Betrieb sind, d.h. keine Verzögerungen in den Schichten, perfekte Verfügbarkeit des Rohmaterials, keine Ausfallursachen usw.
- 100 % Leistung würde bedeuten, dass die Geräte immer mit der theoretischen Höchstgeschwindigkeit laufen, was als ideale Zykluszeit bezeichnet wird.
- 100 % Qualität ist gleichbedeutend mit einer Nullproduktion von fehlerhaften Waren. Jedes einzelne produzierte Stück muss perfekt sein.
Die Hersteller streben in der Regel einen OEE-Wert von 80-95 % an, der als ausgezeichnet gilt, aber je nach Branche kann dieser Wert stark variieren.
In der Regel gilt ein OEE-Wert von etwa 60 % als gut, aber verbesserungswürdig.
Es ist zwar wichtig, einen möglichst hohen OEE-Wert anzustreben, aber es ist auch entscheidend, die realistische Produktionskapazität zu berücksichtigen und eine Überschätzung des Potenzials zu vermeiden.
Fallstudien zur OEE-Implementierung
Lassen Sie sich von OEE-Erfolgsgeschichten von Herstellern inspirieren, die erfolgreich OEE-Messsysteme eingeführt und erhebliche OEE-Steigerungen erzielt haben.
Sintex
Sintex ist ein Hightech-Komponentenhersteller aus Dänemark, der die Factbird® DUO-Lösung eingeführt hat. Das Unternehmen begann langsam mit der Installation von Factbirds IIoT-Gateways auf 10 seiner Maschinen. Die IoT-Funktionalität und die flexiblen Konnektivitätsoptionen von Factbird machten es zur perfekten Lösung. Inzwischen hat das Unternehmen Factbird auf 30 seiner Maschinen erweitert.
Nachdem wir den Factbird® DUO installiert hatten, hat er uns sofort die Augen geöffnet. Wir wussten nicht, dass das System so schnell so positive Auswirkungen haben würde... Wir hatten viele kleine Stopps, die vor Factbird schwer zu erkennen waren, aber wir haben festgestellt, dass diese Stopps einen größeren Einfluss auf die Produktion hatten als die längeren Stopps.
Casper Levorsen - Produktionstechniker bei Sintex A/S
Mit Factbird war Sintex in der Lage, die dringlichsten Stopp-Ursachen zu identifizieren und somit schnelle, faktenbasierte Entscheidungen zu treffen, die innerhalb der ersten Woche zu einer Effizienzsteigerung von 5% führten.
Lesen Sie die ganze Geschichte von Sintex >
Royal Unibrew
Royal Unibrew ist eine internationale Brauerei mit Hauptsitz in Faxe, Dänemark. Sie gilt als das zweitgrößte Bierunternehmen Dänemarks mit einer starken Präsenz in den baltischen Ländern. Zu den Marken im Portfolio von Royal Unibrew gehören Faxe, Ceres, Royal, Albani, Vilniaus Tauras und Kalnapilis. Sehen Sie sich das Video an und erfahren Sie, wie das Unternehmen die OEE-Messlösungen von Factbird eingeführt hat.