Was sind die 8 Verschwendungsarten der schlanken Produktion und wie kann man sie reduzieren?
In diesem Leitfaden stellen wir das Konzept der schlanken Produktion vor, wobei wir auf die so genannten 8 Verschwendungsarten eingehen und erläutern, wie Unternehmen diese vermeiden können.
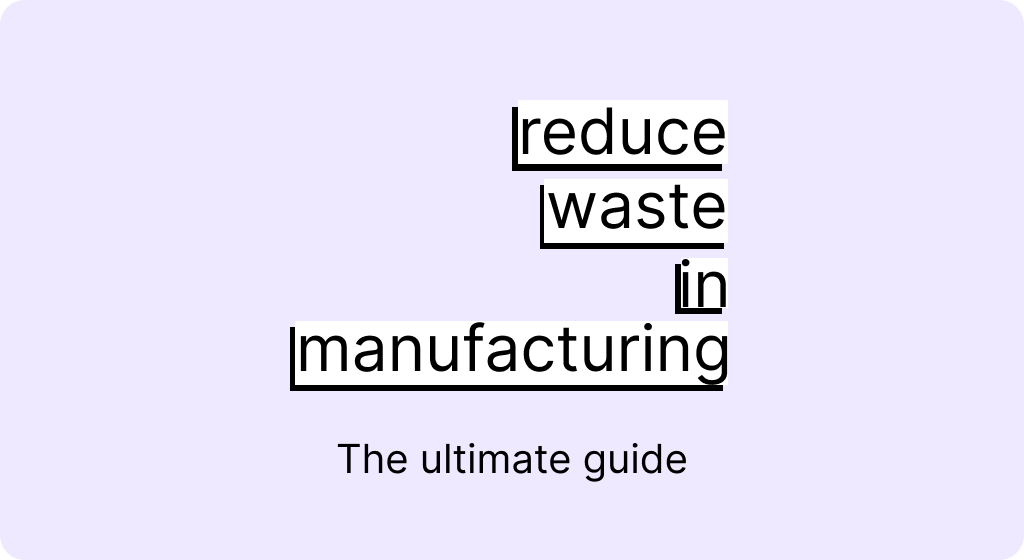
Effizienz ist das Herzstück von Fertigungsprozessen. Da wir uns auf kohlenstofffreie Prozesse zubewegen und eine nachhaltige Produktion im Auge behalten, ist es an der Zeit, sich mit den Auswirkungen der Verschwendung in der Fertigung zu befassen. Die oberste Priorität der Manager ist die Beseitigung von Abfällen in industriellen Prozessen, aber wie können wir die Bereiche ausfindig machen, in denen Ressourcen falsch eingesetzt werden?
In diesem Leitfaden stellen wir die Konzepte der schlanken Produktion vor, wobei wir die so genannten 8 Verschwendungen von Lean hervorheben und erläutern, wie Unternehmen diese durch Industrie 4.0-Softwarelösungen vermeiden können.
Was ist Lean Manufacturing?
Lean Manufacturing ist eine Produktionsmethodik, die auf die Maximierung der Produktivität bei gleichzeitiger Reduzierung der Verschwendung ausgerichtet ist. Es gibt mehrere damit zusammenhängende Begriffe, wie schlanke Produktion und Lean. Historisch gesehen können wir die Modelle JIT (Just-in-Time) und TPS (Toyota Production System) als Vorläufer der Lean-Methode bezeichnen.
Fünf Säulen bilden die Kernprinzipien dieser Methodik, die auch als die fünf Lean-Prinzipien bekannt sind. Diese wurden in James P. Womack und Daniel T. Jones' Buch "Lean Thinking: Verbannen Sie Verschwendung und schaffen Sie Wohlstand in Ihrem Unternehmen" (1996)
Grundsatz Nr. 1 - Den Wert definieren
Wir können den Wert als die Summe annehmen, die ein Kunde für ein Produkt oder eine Dienstleistung zu zahlen bereit ist. Bei technologischen Gütern ist dies möglicherweise nicht offensichtlich, da die Produkte die Erwartungen der Kunden übertreffen, und hier hilft die Befriedigung eines Bedürfnisses, den Wert zu definieren.
Unternehmen legen den Wert eines Produkts oder einer Dienstleistung nicht zufällig fest. Da die Hauptabsicht hinter der Produktion darin besteht, dem Endkunden einen Mehrwert zu bieten, können verschiedene Techniken wie Interviews, Marktforschung, Konkurrenzanalysen, Umfragen und demografische Informationen den Unternehmen dabei helfen, die Bedürfnisse der Kunden, ihre Bereitschaft, für eine Lösung zu zahlen, und das Potenzial, das sie auf einem bestimmten Markt haben kann, zu ermitteln.
Prinzip Nr. 2 - Abbildung des Wertstroms
Nach der Festlegung des Wertes ist es an der Zeit, diesen als Referenzpunkt zu verwenden und die potenziellen Bereiche zu finden, die diesen Werten entsprechen. Bis zu diesem Punkt ist es an der Zeit, die Prozesse und ihre Abfallproduktion zu bewerten, die in zwei Gruppen eingeteilt werden können: nicht wertschöpfende, aber notwendige Abfälle und nicht wertschöpfende und unnötige Abfälle. Die zweite Gruppe sollte sofort aus der Produktion entfernt werden.
Kanban-Tafeln (die durch das TPS-Modell entstanden sind) sind wertvolle Hilfsmittel, um diesen Wertstrom abzubilden, und er sollte in diesen Kategorien angeordnet werden:
- Angefordert
- In Arbeit
- Erledigt
Indem Sie den Arbeitsablauf mit Hilfe einer Kanban-Tafel organisieren, können Sie leicht erkennen, in welchen Bereichen der Produktion Verschwendung anfällt. Ein weiterer Vorteil ist, dass sie zur Optimierung der Arbeitsabläufe beitragen, da die Mitarbeiter Engpässe leicht erkennen können.
Prinzip #3 - Fluss schaffen
Wenn Verschwendung in unserem Produktionsprozess keine Rolle spielt, müssen wir sicherstellen, dass alles reibungslos und ohne Verzögerungen oder Unterbrechungen abläuft. Deshalb kann der Einsatz von Instrumenten wie Kanban-Tafeln helfen, da wir so verhindern können, dass größere Ereignisse, die Zeit und Ressourcen von unseren Produktionslinien abziehen, blockiert werden.
Engpässe sollten angegangen und überprüft werden, um ihre Hauptursachen zu klären, und dann sollte der Prozess für weitere Verbesserungen neu bewertet werden. Eine einfache Möglichkeit, solche Situationen zu lösen, besteht darin, die Arbeitsbelastung zu begrenzen, bis der Engpass behoben ist. Die Verwendung von WIP-Limits (Work-in-Process-Limits) unterstützt diese Idee, da es sich dabei um feste Beschränkungen handelt, die helfen können, Prozessverschwendung zu identifizieren.
Vermeiden Sie um jeden Preis Praktiken wie Multitasking, um die Qualität Ihrer Produktion nicht zu gefährden.
Prinzip Nr. 4 - Pull aufbauen
Anstatt produzierte Waren zu horten, setzt die schlanke Produktion auf ein begrenztes Produktionssystem, bei dem neue Elemente nur dann hergestellt werden, wenn freie Lagerkapazitäten vorhanden sind. Dies verhindert eine Überproduktion und senkt die Kosten, da der Preis, den die Kunden zahlen, dem tatsächlichen Wert entspricht, den sie benötigen.
Bei der Arbeit in einem Pull-System werden die Aufgaben in eine Warteschlange eingereiht. Wenn ein Arbeiter oder eine Maschine untätig ist, muss die nächste zu vergebende Aufgabe die höchste Priorität in dieser Warteschlange haben. Die Hersteller können dann die Effizienz der Produktionsprozesse anhand der Zykluszeiten (und im Vergleich zu den idealen Zykluszeiten) und der Durchsatzkapazität messen.
Es gibt drei verschiedene Arten von Full-Pull-Produktionen:
- Supermarkt-Pull-System: Der einfachste Typ. Sobald ein Produkt an seinen endgültigen Bestimmungsort geliefert wurde, wird es aus dem verfügbaren Bestand entnommen. Dann gibt dieses Pull-System den Auftrag, eine neue Einheit zu produzieren.
- Sequentielles Zugsystem: Ist vorgesehen, wenn der Bestand schwer zu verfolgen ist. Daher wird die Produktion nach Bedarf abgewickelt (Produkt wird auf Bestellung hergestellt). Die Einschränkung dieses Pull-Systems ist, dass es komplexe Managementfähigkeiten erfordert, um den Produktionsfluss aufrechtzuerhalten.
- Gemischtes Supermarkt/Sequential-System: Es funktioniert, wenn ein kleiner Prozentsatz der Teile den Großteil des täglichen Produktionsvolumens ausmacht.
Grundsatz Nr. 5 - Auf ständige Verbesserung hinarbeiten
Es gilt als das wichtigste Prinzip der schlanken Produktion, da es eine Änderung der Denkweise impliziert. Kontinuierliche Überarbeitung und Forschung zur Verbesserung von Prozessen werden Teil der Unternehmenskultur, in der jeder Mitarbeiter nach Perfektion streben sollte, ohne die Anforderungen des Kunden zu vernachlässigen.
Methoden wie die Plan-Do-Check-Act-Methode sind wertvolle Werkzeuge, um diese Denkweise der ständigen Verbesserung in jeder Organisation umzusetzen. Es ist jedoch auch ratsam, mit anderen Strategien zu arbeiten, z. B. mit Stand-up-Meetings.
Was sind die 8 Verschwendungsarten in der schlanken Produktion?
Im Mittelpunkt der schlanken Produktion steht die Reduzierung von Verschwendung. Im Folgenden werden die 8 Verschwendungsarten in der schlanken Produktion beschrieben.
1. Defekte
Sie werden in der Regel als Ausschuss in der Produktion betrachtet, d. h. als jede Verformung oder unerwünschte Eigenschaft eines Produkts, die bei einer Inspektion festgestellt wird. Obwohl einige Teile nachbearbeitet werden können, zielt die schlanke Produktion auf eine "Right-First-Time"-Produktion ab, was bedeutet, dass die Zeit effizient genutzt wird.
Die Lösung: Dank der Einführung einer Produktionsüberwachungssoftware kann die Anzahl der Ausschussteile erheblich reduziert werden, wodurch Verschwendung vermieden und die OEE-Werte verbessert werden.
2. Überproduktion
Mehr Waren zu produzieren, als die Nachfrage erfordert, ist eine Verschwendung von Zeit, Mühe und Ressourcen. Wie wir in der Definition der schlanken Produktion eingeführt haben, besteht ein Grundsatz der schlanken Produktion darin, nur so viel zu produzieren, wie unsere Lagerkapazität zulässt.
Lösung: Bereiten Sie Ihr Team auf eine JIT-Mentalität vor, d. h. die Produktion wird erst dann aufgenommen, wenn die Bestände wieder aufgefüllt werden müssen. Wenn es Leerlaufzeiten gibt, sollten Sie dieses Humankapital und diese Zeit in die Erprobung innovativer Lösungen stecken, die Ihre Leistung verbessern können.
3. Warten
Zeit ist die wertvollste Ressource in der Fertigung, da Leerlaufzeit gleichbedeutend mit fehlender Produktion ist. Wann immer eine Maschine einen Stopp verursacht, der länger als 10 Sekunden dauert, oder einen kumulierten kleineren Stopp während des Tages hat, können wir sicher sein, dass dies ein verpasster Tag bei den Produktionsmeilensteinen ist. Doch auch wenn das Warten in der Warteschlange wie ein nicht enden wollender Kaskadenprozess erscheinen kann, wird eine Marge als akzeptabel angesehen und der Überproduktion vorgezogen.
Lösung: Suchen Sie nach den Ursachen für Engpässe und beseitigen Sie die angesammelten Mikrostopps. Hersteller übersehen oft Stopps zwischen 2-3 Sekunden, aber ihre Wiederholung kann zu erheblichen Verzögerungen führen.
4. Transport
Der Transport von Teilen oder Fertigprodukten unterliegt in der Regel nicht denselben strengen Richtlinien wie andere Prozesse in Ihrem Werk. Eine Vernachlässigung der Sorgfalt beim Transport kann zu unnötigen Fahrten, beschädigten Teilen und Verschwendung von Zeit, Kraftstoff und Personal führen.
Lösung: Nehmen Sie sich besonders viel Zeit, um detaillierte Routen für den Transport von Teilen innerhalb Ihrer Fabrik zu planen. Die beteiligten Mitarbeiter, das Inventar, die Ausrüstung, die Produktlinien usw. sollten in diesem Plan detailliert aufgeführt werden, damit die Routen so optimiert werden können, dass unterschiedliche Anforderungen auf derselben Route abgedeckt werden, ohne die Lieferzeiten zu beeinträchtigen.
5. Bestandsaufnahme
Die Verschwendung von Lagerbeständen hängt mit der Überproduktionsverschwendung zusammen, d. h. mit überschüssigen Vorräten, deren Unterbringung zusätzlichen Platz oder Transport erfordert.
Die Lösung: Der Einsatz von Kanban-Tafeln hilft, den Fluss der produzierten Waren effektiv zu verwalten. Auf diese Weise können die Manager die Gesamtzahl der gelagerten Teile erfassen und eine Überproduktion verhindern.
6. Nicht genutzte Personen
Diese Verschwendung ist schwer zu beheben, da sie eine erfahrene Führungskraft erfordert, die für das Personal verantwortlich ist. Wenn die Fähigkeiten einer Person nicht in vollem Umfang genutzt werden, kann es zu diesen drei potenziellen Problemen kommen:
- Mangelnde Motivation zur Arbeit
- Mangelnde Leistung des Arbeitnehmers
- Vergeudung von Wachstumspotenzial für das Unternehmen und die Karriere des Mitarbeiters
Diese Verschwendung hat aber auch eine Kehrseite, nämlich dann, wenn die betreffende Person mit Aufgaben überlastet ist, die mit ihrem Talent nichts zu tun haben. Infolgedessen bleiben die Prozesse stecken, und das Unternehmen verliert seinen Fluss.
Die Lösung: Gehen Sie auf das Potenzial und die Fähigkeiten Ihrer Belegschaft ein, indem Sie bei der Einstellung eines Bewerbers ausführliche Gespräche führen. Bei Mitarbeitern, die bereits zum Unternehmen gehören, sollten die HR-Teams deren Leistung verfolgen und nach freien Stellen suchen, die im Unternehmen besetzt werden können, um dem Mitarbeiter die Möglichkeit zu bieten, sich beruflich weiterzuentwickeln.
Stellen Sie unbedingt Assistenten für Funktionen ein, die viele sich wiederholende Aufgaben erfordern, die den Fokus des Mitarbeiters von den Bereichen ablenken, in denen er einen Mehrwert schaffen kann. Wenn die Einstellung von Personal keine Option ist, sollten Sie Softwarelösungen in Betracht ziehen, die zur Automatisierung von Prozessen beitragen können.
7. Antrag
Bewegungsverschwendung liegt vor, wenn eine Handlung ausgeführt wird, die keinen Mehrwert für das Produkt darstellt. Zum Beispiel, wenn ein Bediener sich hin und her bewegen muss, um die benötigten Werkzeuge für den Arbeitsplatz zu holen, weil der Lagerplatz nicht ausreicht, um sie alle unterzubringen.
Die Lösung: Verhindern Sie diese Verschwendung, indem Sie die Leistung der Bediener während der Schicht beobachten und schlechte Ergonomie angehen. Dadurch werden sowohl Zeitverschwendung als auch mögliche Arbeitsunfälle vermieden.
8. Extra Verarbeitung
Die zusätzliche Bearbeitung ähnelt einem Antrag in Bezug auf Maßnahmen, die keinen zusätzlichen Wert für das Produkt bringen, sondern sich speziell auf Materialänderungen oder ästhetische Merkmale beziehen. Mit dieser Verschwendung können wir Änderungen der Beschichtung, Änderungen der Verpackung und Prozesse assoziieren, die einen beträchtlichen zusätzlichen Zeitaufwand bei geringer Veränderung des Produkts erfordern, usw.
Die Lösung: Bevor Sie sich in eine ästhetische Veränderung Ihrer Produktlinie stürzen, sollten Sie sich fragen, ob die Veränderung den Aufwand wirklich wert ist. Wenn Änderungen nur aus Perfektionismus vorgenommen werden, aber keinen Mehrwert für das Produkt bringen, sollten Sie sie ausschließen. Umfragen können ein wertvolles Hilfsmittel sein, um herauszufinden, ob eine Änderung erforderlich ist, damit ein Produkt mit der Konkurrenz mithalten kann.
Wie können wir die Produktion mit Lean-Prinzipien optimieren?
Der Grundgedanke der schlanken Produktion ist die Optimierung der Prozesse und die Beseitigung von Verschwendung. Zur Vereinfachung der 8 Verschwendungsarten bei Lean können wir die Verschwendung in der Produktion in die Kategorien Talent, Zeit und materielle Güter einteilen.
Talent
Um die Talente zu optimieren, sollten wir uns zunächst darauf konzentrieren, welche Aufgaben durch Software automatisiert werden können, so dass weniger Personal für banale Aufgaben wie das manuelle Zählen benötigt wird. Aber auch die Manager müssen sich mit den Fähigkeiten ihrer Mitarbeiter auseinandersetzen.
Es ist wichtig, die richtigen Schulungen anzubieten und die Bereitschaft zur ständigen Verbesserung zu fördern. Einige der größten Zeitverschwendungen sind darauf zurückzuführen, dass Mitarbeiter nicht für die Aufgaben geschult werden, die sie ausführen sollen, oder dass neue Maschinen auf den Markt kommen und sie diese nicht verstehen.
Die Verbesserung Ihrer Prozesse beginnt mit der Verbesserung der Arbeitsweise Ihrer Mitarbeiter.
Zeit
Die Untersuchung von Engpässen und deren Ursachen hilft, Verzögerungen fast vollständig zu beseitigen. Die Neugestaltung Ihrer Produktionsstrategie, um die idealen Zykluszeiten zu erreichen, ist eine weitere Möglichkeit, die Lean-Prinzipien auf die Fertigung anzuwenden, mit dem zusätzlichen Nutzen eines höheren Durchsatzes.
Die Datenerfassung und -berichterstattung ist zeitaufwändig und kann durch KI-gestützte Lösungen erledigt werden. Dadurch müssen die Bediener solche Aufgaben nicht mehr manuell durchführen, was den Faktor "menschliche Fehler" verhindert.
Tangibles
Die Überbeanspruchung von Maschinen führt zu Bruch, was bei Lean gleichbedeutend mit Ausfallzeiten ist. Wie viele Ressourcen in Form von Rohstoffen, Werkzeugen, Zeit, Energie usw. verschwenden wir pro Monat? Das ist eine interessante Frage, die sich Manager stellen können.
Die Anwendung der Lean-Methode in der Produktion kann die Effizienz der Prozesse während einer Betriebszeit erheblich steigern und die Notwendigkeit endloser Schichten, in denen die Maschinen aufgrund von Überlastung verrotten, verringern.
Welche Software können Unternehmen nutzen, um Lean in der Produktion einzuführen?
Mehrere Lösungen können Einblicke in den Produktionsprozess bieten. Die Datenerfassung ist vor der Umsetzung jeder Art von Strategieänderung von entscheidender Bedeutung, erst recht bei der schlanken Produktion.
Es gibt verschiedene Ansätze, wie Software bei der Umsetzung von Lean helfen kann. Die Fertigungsbedarfsplanung (MRP) ist eine der Optionen, die man in Betracht ziehen kann, da diese Systeme sowohl die Produktion als auch den Bestand überwachen.
Cloud-basierte Produktionsüberwachungssoftware ist die ideale Lösung, da sowohl die Mitarbeiter als auch das Management rund um die Uhr Daten abrufen können, ohne selbst in der Werkstatt anwesend sein zu müssen. Diese Lösungen sind mit KI-Technologie ausgestattet und nutzen Sensordaten, um auf der Grundlage von Fakten Verbesserungsmöglichkeiten zu analysieren und vorzuschlagen.
Factbird und Lean Manufacturing Fallstudie
Factbird ist eine Industrie 4.0-Software zur Produktionsüberwachung, die über die Verfolgung von OEE-Kennzahlen hinausgeht. Da wir Live- und historische Daten verfolgen können, sind Manager in der Lage, Strategien zur Produktionsoptimierung auf der Grundlage der gesammelten Daten zu verfolgen. Die Endleistung dieser Entscheidungen kann sofort mit Live-Daten analysiert und mit den Ausgangswerten verglichen werden. Und das Beste daran? Blackbird ist mit anderen Technologielösungen für ERP (SAP, Oracle, etc.), OPC und PLC kompatibel.
Im Falle der schlanken Produktion möchten wir kurz die Anwendergeschichte unseres Kunden Autins vorstellen, einem führenden Industriedesigner, Hersteller und Lieferanten von Schall- und Wärmedämmungslösungen für die Automobilindustrie und andere Branchen. Als die COVID-19-Pandemie zuschlug und Beschränkungen eingeführt wurden, mussten viele Hersteller erhebliche Nachfragerückgänge hinnehmen. Daher musste eine neue Strategie entwickelt werden, um zu überleben.
Eine der größten Herausforderungen, mit denen Autins konfrontiert war, waren die erheblichen Arbeitskosten. Trotz einiger progressiver Schritte in Richtung einer schlanken Produktion durch den Betriebsleiter in Deutschland fehlte es an einem klaren Bild der Maschinenleistung. Nach einer ersten Besprechung wurde das Projekt mit sehr klaren Zielen gestartet:
- Zuverlässige Daten und ein klares Bild der aktuellen Produktionseffizienz
- Steigerung der Produktivität in den beiden Hauptmaschinen
- Erhalten Sie Echtzeitdaten über Schichten
- Verstehen Sie die Gründe für den Stillstand von Maschinen
Das Factbird-System war einfach zu installieren und wurde vom Autins-Team durchgeführt, da die Einschränkungen durch die Pandemie kein zusätzliches Personal zuließen. Wir begannen mit einem Pilotprojekt auf den beiden Hauptmaschinen. Das Feedback zu unserer Factbird-Lösung kam sowohl von Daten als auch von visuellen Informationen.
Autins bemerkte sofort ein störendes Muster in der Produktion aus früheren Perioden, und das Ziel war, diese Prozesse zu stabilisieren. Auf diese Weise fand bei den Bedienern ein deutlicher Bewusstseinswandel statt, da sie verstanden, dass das Hauptziel darin bestand, eine zuverlässige und stabile Produktion zu erreichen und nicht die Produktionszahlen zu steigern. Die Bediener arbeiteten zusammen, um herauszufinden, welche Bereiche anhand des Datenfeedbacks verbessert werden konnten, und ergriffen in wichtigen Fällen Maßnahmen. Einer davon ist die Materialumstellung - ein Prozess, der überdacht werden sollte.
Seit der Implementierung der Factbird Technologie hat Autins seine Schichten von 3 auf 2 reduziert und benötigt keine zusätzliche Zeit mehr, um die Produktionsanforderungen zu erfüllen. Die OEE konnte in nur 3 Monaten um 27 % gesteigert werden.
Wie setzt Factbird die Lean-Prinzipien um?
Zunächst müssen wir die Lean-Methode als einen schrittweisen Prozess verstehen. Veränderungen werden nicht von heute auf morgen eintreten; daher ist es ein zweistufiger Prozess:
- Umsetzung von Technologieänderungen durch den Einsatz von IoT-Software zur Produktionsüberwachung
- Mentalitätswandel dank der Bereitstellung zuverlässiger Daten
Unsere Erfahrung aus zahlreichen Erfolgsgeschichten von Kunden ist, dass der Einsatz von Factbird in weniger als 3 Monaten eine dramatische Leistungssteigerung bedeutet. Manchmal sind die Ergebnisse sogar schon nach einer Woche sichtbar.
Die Qualitätskontrolle ist automatisiert, d. h. die Ausschusszählung muss nicht manuell von den Bedienern durchgeführt werden (und spart somit wertvolle Zeit). Bediener und Manager können sowohl Daten als auch visuelle Daten von unseren Sensoren und Kameras abrufen. Das Videomaterial wird von der Factbird-Lösung analysiert und gibt Aufschluss darüber, in welchen Bereichen die Produktion ohne große Investitionen optimiert werden kann.
Sie können sicher sein, dass Ihre Daten sicher sind, denn die hochgeladenen Daten werden über verschlüsselte SSL-Verbindungen verwaltet. Nur autorisierte Logins können die mit unseren Servern geteilten Daten überprüfen, und diese Informationen sind rund um die Uhr verfügbar, unabhängig vom verwendeten Gerät.
Abschließende Überlegungen
Maßnahmen gegen die Verschwendung in der Produktion sind der Schlüssel, um auf dem Markt bestehen zu können. Nur Unternehmen, die keine hohen Produktionskosten haben, verfügen über genügend Spielraum, um ihre Preisspannen bequem zu verwalten, ein Vorteil, der die Kundenbindung garantiert.
Wie wir gesehen haben, ist Verschwendung in der schlanken Produktion der Feind, den es zu bekämpfen gilt, und dank der Lösungen zur Produktionsüberwachung kann die Umsetzung dieser Strategien ohne großen Aufwand erfolgen. Bedenken Sie den Mehrwert für Ihr Produkt, wenn die Kunden die Bemühungen um bestmögliche Qualität anerkennen und gleichzeitig den ökologischen Fußabdruck, der hinter der Herstellung steht, verringern. Wir hoffen, dass dieser Leitfaden Ihnen einen Einblick in den Wert der Abfallproduktion im Rahmen des Lean Management geben kann.