Calculating throughput: A guide for increasing production performance
Estimating your factory’s efficiency involves a significant number of elements, but throughput remains the metric that defines a competitive edge.
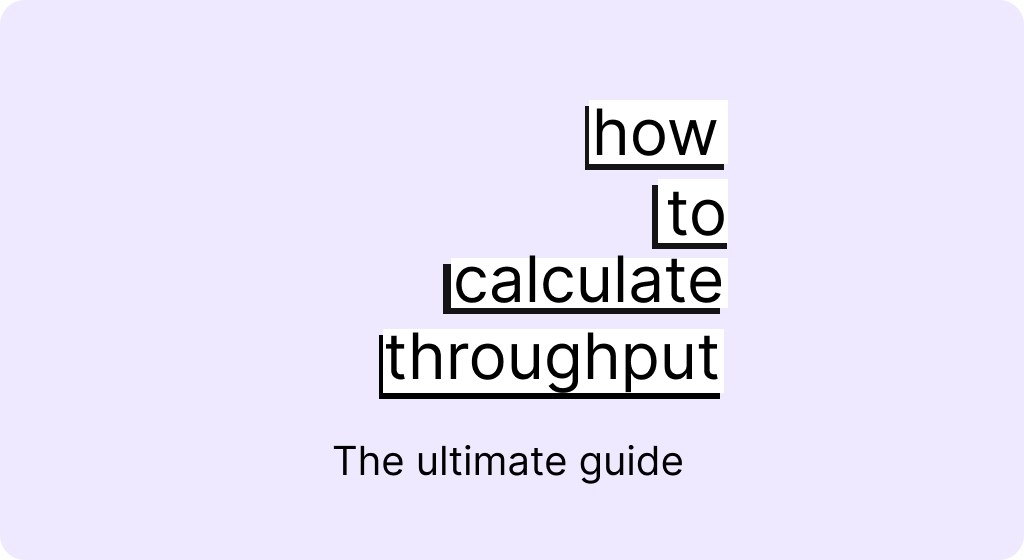
Estimating your factory’s efficiency involves a significant number of elements, but throughput remains the metric that defines a competitive edge. It is so relevant that OEE calculations bring insights into whether the factory’s potential throughput is restricted. For that reason, throughput directly affects the revenue rate and impacts strategies for upcoming investments.
With this guide, we shall introduce a methodology to calculate throughput and the different variables that define its importance in everyday production.
What is Throughput?
Throughput rate is the metric by which we measure the rate at which units move through the production process, from the start point to the completed unit. It can involve a number of elements, from raw materials transportation, material processing, development of individual parts, assembly of units, interactions with operators, customer input (in the case of custom-made production), etc.
Two elements make the throughput rate calculation:
Inventory (I): This stands for the number of units on the shop floor rather than the finished products sent to delivery. It may seem a bit difficult to understand as it shifts the typical “completed product ready to sell” count, listing also the units in the production stage.
Flow Time (T): The amount of time a product spends, from start to finish, in production. Flow time is the sum of four different intervals:
- Processing Time: The time spent in actual production. Covers all the steps from raw material to assembly and finished product.
- Inspection Time: Depending on the industry, the inspection time can drastically change as it may require stress testing, visual quality testing, taste/smell testing (for the food & beverage industry), etc. It is the cumulative time involved in checking components and sub-assemblies in the manufacturing process.
- Move Time: This also depends on the industry, but mostly on how modern the machinery is to minimize the movement/staging processes. Move time includes the time to move sub-assemblies between workstations.
- Queue Time: The time a unit spends in the queue to be processed, inspected, or moved, either a completed product or a sub-assembly. Usually builds up depending on how complex the production process is.
The Importance of Calculating Throughput
Determining the real throughput factories produce is essential to guarantee profit maximization and to improve production workflows. Four aspects help us understand the importance of calculating throughput.
First and foremost, knowing the actual production process time helps us identify the bottlenecks. This is an iterative process, as bottlenecks can change from period to period. Some causes could be linked to machinery, in which production manufacturing software is a solution. In others, extensive analyses spot inadequate processes from operators.
Related to the last point, inefficiencies are easy to address when the machinery isn’t operating at its maximum capacity. This can require changes in inspection time, shortening periods between scheduled maintenance, or changing strategies altogether.
Implementing methodologies for optimal production can seem taxing in some cases, but seeing quick results helps the organization identify with those values. An adequate calculation of the throughput rate is required in lean manufacturing processes, as less time spent in production is reflected in extra time to optimize other processes.
Finally, suppose we aim to reduce inefficiencies. In that case, one key element of the throughput calculation is that by decreasing production time, you reduce uptime for machinery, and that is a reduction in energy expenses and extra working hours for personnel. Reduced material waste is another side consequence of this optimization stage.
Cycle Time vs. Throughput Time
Although related, Cycle Time measures the work time from start to finish for one unit, whereas Throughput Time measures the entire process time, including queues.
In practical application, cycle time is used when your machinery works within expectations. In contrast, throughput time should be used to address potential delays, as it is easier to break the stages of each process to build a product.
Lead Time vs. Throughput Time
Unlike throughput time, Lead Time is a metric based on customer demand. We start counting the lead time when an order is placed, and it stops when the completed product reaches the customer. Companies tend to work with buffers - inventories of products - to reduce lead time drastically; otherwise, it would build insane queue time per customer. The volume of that inventory is directly linked to production capacity, storage capacity, sales strategy, and overall product demand.
On the other hand, throughput time covers the entire production time per item; for that reason, we have to differentiate between batch throughput time and unit product time.
How to Calculate Throughput
The throughput rate is relatively easy to calculate once you have an exact sum of the flow time.
T = I / F
Where:
- T = Throughput
- I = Inventory
- F = Flow time
Still, we must establish the difference between Process Throughput, which is the equation shown above, and Line Throughput.
Process throughput represents the number of good units produced from beginning to end. This takes into account scraps and other issues that can arise during manufacturing processes, such as:
- Downtime (linked to stopping causes)
- Machine speed
- Jamming
- Human factors (operator error or incorrect operator training)
- Lack of raw material
Therefore, if we say a factory has 19,000 units produced per shift, but only 16,400 were right-first-time production, then the throughput rate calculates 16,400 per shift (8 hours), which means 2,050 units per hour. Evidently, numbers, as in this case, help us acknowledge room for improvement in manufacturing processes.
Line throughput represents the produced goods per line per unit of time, but it has to consider the efficiency at which each line operates. For that very reason, we can have different line throughput values but one overall process throughput per shop floor. The importance of line throughput is for addressing machinery efficiency, if they require upgrades, automatization, or if any other relevant failures hinder efficiency.
How to Increase Throughput Rate
When manufacturers spot a hidden potential in their factories, this is a commonly asked question. Throughput rates can either make it or break it when it means satisfying customers or preserving a competitive edge in the market.
In this section, we shall enumerate some strategies to increase your throughput rate for maximum productivity.
Strategy #1 - Eliminating Bottlenecks
As priory mentioned, bottlenecks are easy to identify thanks to throughput analysis. Processes could build up idle time due to machinery malfunctioning or workers not understanding its operation. Other, not so apparent, bottlenecks can be linked to packaging processes or machines not properly syncing queues between workstations.
Eliminating bottlenecks involves evaluating your processes in detail. Finding ways in which optimization can cut production times or eliminating a process entirely for a more cost-benefit solution.
Strategy #2 - Increasing Availability
As we remember from the OEE calculation formula, Availability is one of its components. The two losses in availability are planned and unplanned stops. Planned stops are required during changeovers, for scheduled maintenance, and sometimes during inspections. It is in the unplanned stops category where we can influence.
One common mistake that settles machinery prone to unplanned stops is delaying scheduled maintenance for continuous production. Worn-out machinery or broken pieces of equipment are among the principal reasons why we come across repetitive stop causes.
Train your operators to register the stop causes and the standard troubleshooting procedures. Keeping a historic backlog helps to address reiterative error codes and provide detailed information to the maintenance teams.
Strategy #3 - Reduce Scrap Count
Going back to the example of Throughput Rate calculation, we had a factory producing 19,000 pieces each 8 hours, of which 16,400 were acceptable according to the “right-first-time” principle of OEE. This implies 86.31% of acceptable production or 13.69% in waste.
Management's responsibility is to address waste in manufacturing, so by decreasing the rejection rate by half, you obtain 1300 more pieces per shift. In a factory with four shifts a day, that translates into 5200 pieces more per day, or 27% of the production of one shift. Yes, numbers can make the message sink in when you analyze how much production is literally going to waste due to inefficient manufacturing procedures. Adjustments also help financials by decreasing the cost of reprocessing parts, energy waste, raw material consumption, and extra working hours for your personnel.
Strategy #4 - Reviewing Production Workflows
It is impossible to guess which areas should be improved without acknowledging what's happening on the shop floor. Start by reviewing the personnel working in each area, if their work can be automated or if they are mismatched in terms of skills. Knowing the weekly production goals and overall work plan is vital to align the production objectives across all factories.
Regarding equipment, evaluate these aspects:
- Status and working performance
- Availability of replacement parts
- Cost of scheduled maintenance
- Requirement of specialized maintenance crews
- Possibility of automating production
- Implementing production monitoring software
- Investing in new machinery
The third stage, which refers to processes, is linked to bottlenecks. On this point, you can also evaluate transportation to storage facilities in terms of time and resources required, as well as the ideal production volume to meet consumers’ demands.
Strategy #5 - Invest in Employee Training
The best prepared your personnel is, the more confidence they have when troubleshooting stop causes or making decisions based on reliable data. Experience does tell us that operators who lack the required training are prone to trigger production delays, which ripples in the supply chain.
Instead, opt for a continuous improvement mentality across all levels in your organization. Prepare periodic training sessions that coach your operators on new technologies or methodologies to improve existing work practices.
How can Factbird Benefit Companies Regarding Throughput and General Manufacturing Optimization?
Manufacturing monitoring offers plenty of advantages to factories, starting by seeing changes in OEE and throughput rates without requiring hefty investments. Thanks to monitoring solutions like Factbird, legacy machinery can be integrated into networks for increased production, where management or operators can access information at any point. In turn, business owners are not required to invest large sums for increased production.
By using industry 4.0 technologies, we can retrieve detailed information on our production numbers, address where bottlenecks are located, replay failed processes (thanks to using video monitoring solutions like Factbird View), and develop corrective strategies. Automating tasks, such as counting scraps, help us to relocate talent to more relevant positions, reducing delays in availability.