Data-Driven insights, human-driven impact: Examples of data focus and review meetings for each team
In this article, we explore the potential of data in manufacturing and provide guidance on how to leverage digital performance boards with automated analysis.
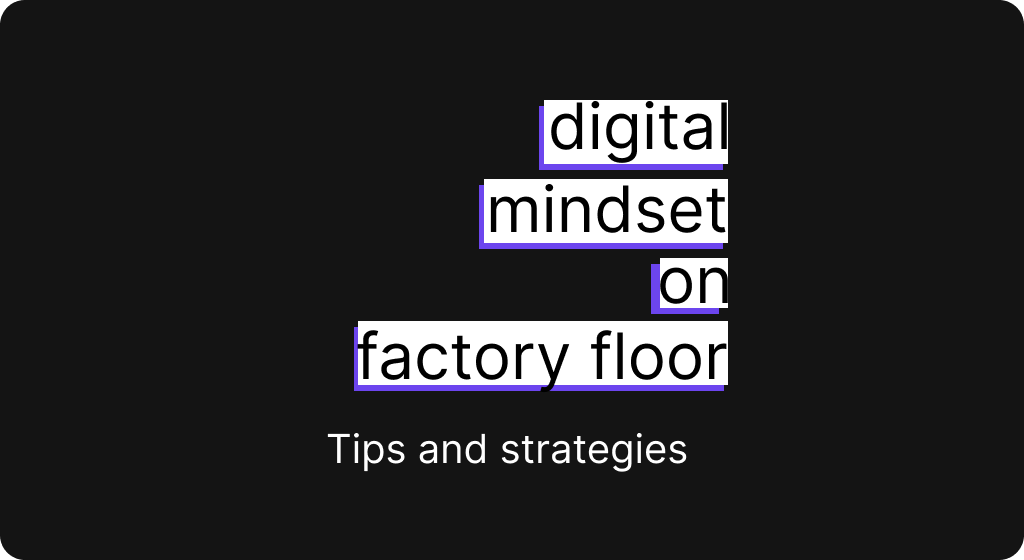
The manufacturing industry has been undergoing a profound transformation through the digitization of operations and the adoption of data-driven techniques. From the operational team to technical experts, team leaders, and support functions, empowering all teams involved with data has become a key driver for enhancing performance and achieving operational excellence.
People, armed with data, possess the knowledge and experience to identify patterns, correlations, and anomalies that may not be evident at first glance. They can contextualize the data, draw connections, and understand the underlying factors influencing performance. Data provides the foundation, but it is people who have the capacity to transform it into actionable insights and tangible improvements.
In this article, we explore the potential of data in manufacturing and provide guidance on how to leverage digital performance boards with automated analysis and reporting capabilities to unlock the power of data across all teams.
Key Questions for Data Empowerment
To ensure data empowerment throughout the organization, several key questions should be considered:
- What data do people need to do a good job?
- When and how will they access this data?
- How will they use it to drive performance?
- How will they be trained to effectively utilize and interpret the data?
By addressing these questions, organizations can develop data-driven strategies that meet the unique needs of each team, function, and individual.
Examples of Data Focus across Teams and Functions
Different teams and functions can benefit from various data sets to optimize their performance. Here are some essential data focuses for each:
Operational Team: Product and machine settings, batch and in-process control data, equipment warnings and alarms, batch target adherence (OEE1&2), changeover time, scrap and eject performance, and the effect of adjustments.
Technical Team: Equipment uptime data (OEE1), downtime pareto analysis, notifications and work orders, maintenance data/system settings, project plans, and production plans, as well as the effect of adjustments.
Team Leaders: Safety, staffing plan fulfillment, production plan adherence, process confirmation status, quality and scrap data, and production key performance indicators (changeover, cycle time).
Support Function: Process data such as out-of-specification incidents, OEE, scrap, deviation data, value stream data (e.g., OTIF), production plans, and trending of quality, delivery, and cost.
Managers: Quality data and complaints trends, value stream OTIF, budget vs. realized, capacity utilization vs. demand, environmental, health, and safety parameters, as well as human resources parameters.
By focusing on these specific data, it is possible to make data-driven decisions and contribute to overall operational excellence.
Harnessing the Power of Data through Regular Review Meeting
Regular review meetings serve as pivotal moments for individuals across various teams and functions to come together and leverage data-driven insights for driving manufacturing improvements. These collaborative sessions create opportunities for different groups to analyze data, exchange perspectives, and collectively develop strategies to optimize performance and achieve operational excellence.
The operational team plays a critical role in utilizing data to enhance performance on the shop floor. Their data review sessions, conducted during shifts at the line, allow them to monitor real-time data, identify trends, and proactively address deviations. By closely examining the data, they can make informed decisions, adjust processes, and drive continuous improvement in their daily operations.
The technical team, with their deep technical understanding and problem-solving skills, engages in data review sessions to assess equipment performance, maintenance schedules, and project plans. Their daily 24-hour team reviews, along with the leader's daily review at the factory level, enable them to analyze data trends, identify potential issues, and implement corrective actions promptly. Additionally, their weekly trend reviews help identify long-term patterns and make strategic decisions to optimize technical processes.
Team leaders, responsible for managing both processes and people, actively participate in data reviews to drive improvements within their teams. Their daily 24-hour reviews conducted with the team and the leader's daily reviews at the factory level allow them to assess real-time performance, identify challenges, and provide the necessary support. The weekly trend review enables them to analyze performance over time and develop targeted strategies to enhance overall team performance.
Support functions, known for their pivotal role in improvement projects, new product entry and product development. Their daily 24-hour team reviews, along with the leader's daily review at the factory level, help them identify opportunities for improvement and align their support activities with the broader organizational goals. The weekly trend review provides insights into long-term trends and assists in developing proactive measures to drive continuous improvement.
Managers, with their comprehensive view of the organization, engage in data reviews to evaluate overall performance and make strategic decisions. Their leader's weekly trend review allows them to assess performance across different teams and functions, identify areas for improvement, and align strategies to meet business objectives. Additionally, the monthly business review serves as a platform to review key performance indicators, evaluate the impact of improvement initiatives, and refine long-term strategies.
Closing Thoughts
By engaging in regular data reviews at different levels, organizations foster a culture of collaboration, learning, and improvement. These sessions facilitate the collective utilization of data to identify challenges, share best practices, and drive actionable insights. With people at the center of data reviews, organizations can ensure that data-driven improvements are effectively implemented, leading to enhanced operational performance and sustained success in the manufacturing industry.