What are the 8 wastes of lean manufacturing and how to reduce them
In this guide, we introduce the concept of Lean Manufacturing, emphasizing what’s known as the 8 wastes of lean and how companies can prevent them.
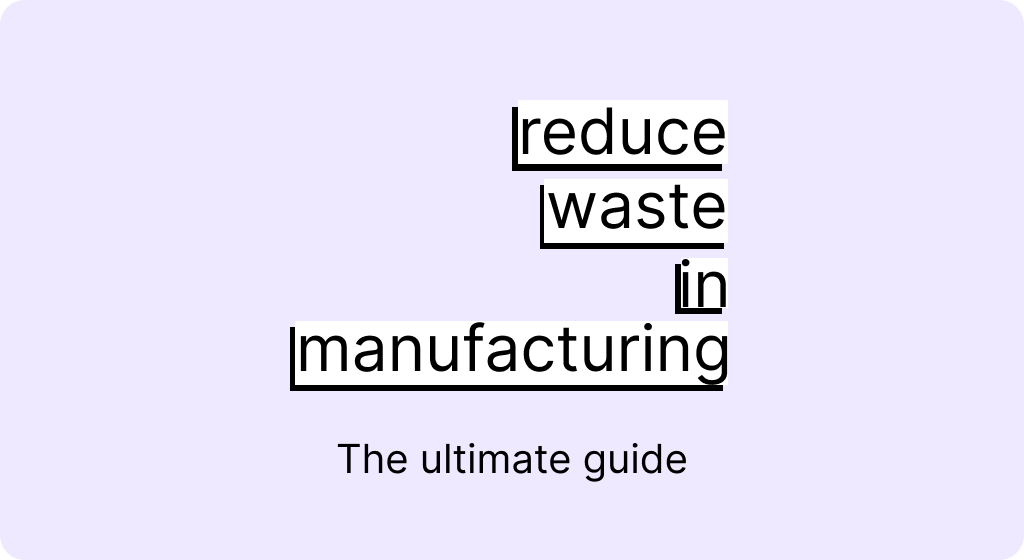
Efficiency is the core of manufacturing processes. As we are moving towards carbon-free processes and keeping a close eye on sustainable production, it is time to address the impact of waste in manufacturing. Managers' first priority is eliminating waste in industrial processes, but how can we locate those areas where resources are misused?
In this guide, we introduce the concepts of Lean Manufacturing, emphasizing what’s known as the 8 wastes of lean and how companies can prevent them through industry 4.0 software solutions.
What is Lean Manufacturing?
Lean Manufacturing is a production methodology focused on maximizing productivity while reducing waste. There are multiple associated terms, such as lean production and lean. Historically, we can reference the JIT (Just-in-Time) and TPS (Toyota Production System) models as precursors to the lean methodology.
Five pillars shape this methodology's core principles, also known as the Five Principles of Lean. These were introduced in James P. Womack and Daniel T. Jones’ book “Lean Thinking: Banish Waste and Create Wealth in Your Corporation” (1996)
Principle #1 - Define Value
We can assume the value as the sum a customer is willing to pay for a product or service. This may not be apparent in the case of technological goods, as products surpass customers' expectations, and this is where serving a need helps define the value.
Companies don’t set the value of any product/service by chance. Since the core intent behind the production is to bring value to the end customer, different techniques such as interviews, market research, competitor’s analysis, surveys, and demographic information can help companies to identify customers’ needs, their willingness to pay for a solution, and the potential it can have in a specific market.
Principle #2 - Map the Value Stream
After establishing the value, it is time to use it as a reference point and find the potential areas that match those values. Up to this point, it is time to evaluate the processes and their waste production, which can be categorized into two groups: non-value waste added but necessary, and non-value waste & unnecessary. The second group should be immediately removed from production.
Kanban boards (which were created by the TPS model) are valuable resources to map this value stream, and it should be arranged in these categories:
- Requested
- In Progress
- Done
By arranging the workflow with the help of a kanban board, you can easily spot the areas of production in which waste is being generated. Another advantage is that they help optimize workflows by allowing workers to spot bottlenecks easily.
Principle #3 - Create Flow
When waste is not an element in our production process, we must ensure everything runs smoothly, without delays or stop causes. This is why using tools like kanban boards can help, as we prevent major event blockers that take both time and resources from our production lines.
Bottlenecks should be addressed, reviewed to clarify their leading causes, and then re-evaluate the process for further improvements. One non-demanding way to solve situations like this is to limit the workload until the bottleneck is sorted out. Using WIP limits (work-in-process limits) boosts this idea, as they are fixed constraints that can help identify process waste.
Avoid, at all costs, practices like multitasking for the sake of your production quality.
Principle #4 - Establish Pull
Rather than hoarding produced goods, lean manufacturing opts for a limited production system in which new elements are elaborated only when there is spare storage capacity. This prevents overproduction and reduces cost, as the price customers pay is the actual value required by clients.
The tasks are slotted in a queue when working in a pull system. When a worker or machine is idle, the next task to be assigned must be the highest priority in that queue. Manufacturers then can measure production processes' efficiency based on cycle times (and compare it with ideal cycle times) and throughput capacity.
There are three different types of full pull productions:
- Supermarket Pull System: The most basic type. Once a product is delivered to its final destination, the product is taken out from the available stock. Then, this pull system orders to produce a new unit.
- Sequential Pull System: Intended when stock is hard to track. Therefore, production is handled by demand (product made by order). The limitation of this pull system is that it requires complex management skills to maintain the production flow.
- Mixed Supermarket/Sequential System: It works when a small percentage of parts respond for the majority of daily production volume.
Principle #5 - Work towards Constant Improvement
It is considered the most important principle of lean manufacturing as it implies a change in mindset. Continuous revisions and research on improving processes become part of the organization’s culture, where every employee should strive for perfection without neglecting the customer’s demands.
Methods such as the Plan-Do-Check-Act are valuable tools to implement this constant improvement mindset in any organization. Still, it is also advisable to work with other strategies, such as stand-up meetings.
What are the 8 wastes in Lean Manufacturing?
At the core of lean manufacturing lies the reduction of waste. The following are the 8 wastes in lean manufacturing.
1. Defects
They are usually considered scraps during production, any deformity or unrequired trait on a product found during an inspection. Although some pieces can be reworked, lean manufacturing aims for “right-first-time” production, which implies time is used efficiently.
Solution: Thanks to the implementation of production monitoring software, scrap count can be significantly reduced, preventing waste and improving OEE values.
2. Overproduction
Producing more goods than what the demand requires is a waste of time, effort, and resources. As we introduced in the lean manufacturing definition, a principle of lean is to produce just the amount that our storage capacity allows us to.
Solution: Prepare your team for a JIT mindset, meaning production will only start when stock needs replenishment. If there is idle time, consider putting that human capital and time into testing innovative solutions that can improve your performance.
3. Waiting
Time has to be the most valuable resource in manufacturing, given that idle time equals no production. Whenever a machine experiences a stop cause that lasts longer than 10 seconds or has an accumulated minor stop during the day, we can be certain that it is a missed day in production milestones. Still, even when waiting can seem like a never-ending cascade process in terms of the queue, a margin is considered acceptable and preferred to overproduction.
Solution: Check for bottleneck causes, and address the accumulated micro stops. Manufacturers often overlook stops between 2-3 seconds, but their reiteration can build up to significant delays.
4. Transportation
Moving parts or finished products usually do not follow the same strict guidelines as other processes inside your factory. Neglecting care in transportation can build up to unnecessary trips, damaged parts, and waste in terms of time, fuel, and human resources.
Solution: Take extra time to plan detailed routes for the transportation of parts inside your factory. Operators involved, inventory, equipment, product lines, etc., should be detailed items in this plan so the routes can be optimized to cover different requirements under the same route while not hindering delivery times.
5. Inventory
Inventory waste is related to overproduction waste, which is any excess supplies requiring extra space or transportation to be accommodated.
Solution: Using kanban boards helps manage the flow of produced goods effectively. That way, managers can address the total count of pieces in storage, preventing extra production.
6. Non-Utilized People
This waste is tough to address, as it requires an experienced manager in charge of personnel. Whenever a person’s capabilities are not used to the full extent, it can build up to these three potential issues:
- Lack of motivation to work
- Lack of performance by the employee
- Wasting growth potential for the company and the employee’s career
There is another side to this waste, and that is when the person is overworked for non-essential tasks related to their talent. As a result, processes get stuck, and the company loses its flow.
Solution: Address the potential and capabilities of your workforce by conducting detailed interviews when hiring a candidate. For employees already part of the company, HR teams should follow up on their performance and look for vacancies that can be filled in-company, offering the employee a chance to grow in their career.
Be sure to hire assistant positions for roles requiring many repetitive tasks that divert the employee's focus from the areas where they can add value. If hiring personnel is not an option, consider software solutions that can help automatize processes.
7. Motion
Motion waste is present when any action that does not add value to the product is performed. Say, for example, when an operator has to move back and forth to grab the required tools for the workstation as there is insufficient storage space to allocate them all.
Solution: Prevent this waste by observing the operators’ performance during shifts, and address poor ergonomics. This shall prevent both time waste and potential work injuries.
8. Extra Processing
Extra Processing is similar to a motion in terms of actions that do not bring any extra value to the product but specifically apply to material changes or aesthetical features. With this waste, we can associate changes in the coating, packaging changes, and processes that require considerable extra time with little change to the product, etc.
Solution: Before jumping into any kind of aesthetic change to your product line, ask yourself if the change is truly worth the effort. If changes are only made out of perfectionism but do not add value to the product, rule them out. Surveys can become valuable resources to research whether a change is required for a product to be up-to-date with competitors.
How can we optimize manufacturing with Lean Principles?
The overall idea behind lean manufacturing is to optimize processes and eliminate waste. To simplify the 8 wastes in lean, we can categorize waste in production as talent, time, and tangibles.
Talent
To optimize talent, we first should focus on which tasks can be automated via software, reducing the need for personnel for mundane tasks such as manual counting. Still, also managers need to address the capabilities of their employees.
Offering the proper training and cultivating a constant improvement mindset is essential. Some of the biggest wastes of time are linked to personnel not being trained for the tasks they are supposed to perform or when new machinery arrives, and they do not understand it.
Improving your processes start by improving how your employees work.
Time
Studying bottlenecks and the reasons behind them helps eliminate delays almost wholly. Redesigning your production strategy to meet the ideal cycle times is another way in which lean principles can be applied to manufacturing, with the added value of increased throughput.
Data collection and reporting is time-consuming and can be handled through AI-powered solutions. This reduces the need for operators to manually perform such tasks, preventing the human-error factor.
Tangibles
Overusing machinery leads to breakage, which equals downtime in lean. How many resources in terms of raw materials, tools, time, energy, and more are we wasting per month? That is an interesting question that managers can ask themselves.
Applying the lean methodology to production can significantly increase the efficiency of processes during an operative time, reducing the need for endless shifts in which machines decay due to overuse.
Which software can companies use to implement Lean in manufacturing?
Multiple solutions can offer insights into what’s going on with the production process. Data collection is vital prior to implement any kind of strategy change, and even more for lean manufacturing.
There are different approaches to how software can help to implement lean. Manufacturing requirements planning (MRP) is one of the options to consider, as these systems monitor both production and inventory.
Cloud-based production monitoring software is the ideal take, as both employees and management can get data 24/7 without even needing to be present on the shop floor. These solutions are powered by AI technology, using sensor data to analyze and suggest improvement areas based on facts.
Factbird and Lean Manufacturing Case Study
Factbird is an industry 4.0 manufacturing monitoring software that goes beyond OEE metrics tracking. Since we can track live and historical data, managers are able to trace strategies for production optimization based on collected data. The end performance of those decisions can be instantly analyzed with live data, contrasting it with initial values. The best part? Blackbird is compatible with other technology solutions for ERP (SAP, Oracle, etc.) OPC and PLC.
In the case of lean manufacturing, we would like to briefly introduce the user story of our customer, Autins, a leading industrial designer, manufacturer, and supplier of acoustic and thermal insulation solutions for the automotive industry and other sectors. As the COVID-19 pandemic hit and restrictions took place, many manufacturers endured significant decreases in demand. Therefore, a new strategy had to take action in order to survive.
One of the biggest challenges that Autins experienced was the considerable labor cost. Despite some progressive steps towards lean manufacturing by their Operation Manager in Germany, the reality was that they lacked a clear picture of machinery performance. After an initial meeting, the project started with very clear objectives:
- Reliable data and a clear picture of the current production efficiency
- Increase productivity in the two primary machines
- Obtain real-time data about shifts
- Understand the reasons why machines stopped
The Factbird system was easy to install and done by the Autins team, as restrictions by the pandemic did not allow extra personnel. We started with a pilot on the two main machines. The feedback from our Factbird solution came both from data and visual information.
Autins instantly noticed a disruptive pattern in production from previous periods, and the aim was to stabilize those processes. By doing so, a significant mindset change happened among operators, as they understood the primary goal was to achieve reliable & stable production, not increase production numbers. Operators worked in cooperation to see which areas could be improvised from the data feedback and took action in significant cases. One of them is material changeover - a process that was due to revisit.
Since the implementation of Factbird’s technology, Autins reduced their shifts from 3 to 2, no longer requiring extra time to meet the production demand. OEE saw an increase of 27% in just 3 months.
How does Factbird deliver on lean principles?
First, we must understand the lean methodology as a gradual process. Changes will not occur overnight; therefore, it is a two-stage process:
- Implement changes in technology by the usage of IoT production monitoring software
- Mindset change thanks to retrieval of reliable data
Our experience in multiple customer success stories is that the usage of Factbird signifies a dramatic performance increase in less than 3 months. Sometimes, results can be seen as quickly as in one week.
The quality checkup is automated, meaning the scrap count does not have to be done manually by operators (hence, saving valuable time). Operators and managers can retrieve both data and visual data from our sensors and cameras. Video footage is analyzed by the Factbird solution, offering insights into which areas the shop floor can be optimized without significant money investments.
Rest assured, your data is secure, as the data uploaded is managed through encrypted SSL connections. Only authorized logins can review the data shared with our servers, and this information is available 24/7, regardless of the device used.
Closing Thoughts
Taking action against waste production in manufacturing is key to staying relevant in the market. Only those companies that do not experience hefty production costs have enough room to manage price ranges with comfort, an asset that certainly guarantees customer retention.
As we have seen, waste in lean manufacturing is the enemy to tackle, and thanks to production monitoring solutions, implementing these strategies can be done without much hassle. Consider the added value to your product when customers acknowledge the efforts to achieve the best quality possible while also reducing the carbon footprint behind that fabrication. We hope this guide can give you insights into the value of addressing waste production in lean management.